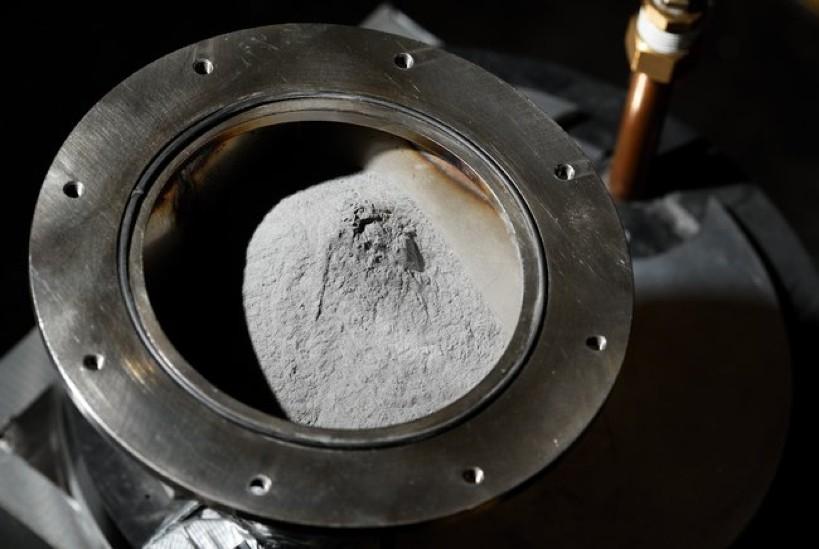
Zukunft im Pulverschnee
Das schwedische Unternehmen VBN Components stellt Stahlprodukte mithilfe additiver Technologien unter Verwendung von Pulver mit Zusatzstoffen her, hauptsächlich Werkzeuge wie Bohrer und Fräser. Die 3D-Drucktechnologie macht Schmieden und Bearbeiten überflüssig, reduziert den Rohstoffverbrauch und bietet Endbenutzern eine größere Auswahl an hochwertigen Materialien.
Das Angebot an VBN-Komponenten umfasst z.B. Vibenite 290der nach Angaben des schwedischen Unternehmens der härteste Stahl der Welt ist (72 HRC). Der Prozess zur Herstellung von Vibenite 290 besteht darin, die Härte der Materialien schrittweise auf bis zu zu erhöhen. Sobald die gewünschten Teile aus diesem Rohmaterial gedruckt sind, ist außer Schleifen oder Erodieren keine weitere Bearbeitung erforderlich. Kein Schneiden, Fräsen oder Bohren erforderlich. So fertigt das Unternehmen Teile mit Abmessungen bis zu 200 x 200 x 380 mm, deren Geometrie mit anderen Fertigungstechnologien nicht herstellbar ist.
Stahl wird nicht immer benötigt. Ein Forschungsteam von HRL Laboratories hat eine 3D-Drucklösung entwickelt. Aluminiumlegierungen mit hoher Festigkeit. Das heißt nanofunktionale Methode. Vereinfacht ausgedrückt besteht die neue Technik darin, spezielle nanofunktionale Pulver auf einen 3D-Drucker aufzutragen, die dann mit einem Laser in dünnen Schichten „gesintert“ werden, was zum Wachstum eines dreidimensionalen Objekts führt. Beim Schmelzen und Erstarren werden die entstehenden Strukturen nicht zerstört und behalten ihre volle Festigkeit, da die Nanopartikel als Keimzentren für die angestrebte Mikrostruktur der Legierung fungieren.
Hochfeste Legierungen wie Aluminium werden häufig in der Schwerindustrie, der Luftfahrttechnik (z. B. Rumpftechnik) und in Automobilteilen eingesetzt. Durch die neue Technologie der Nanofunktionalisierung erhalten sie nicht nur eine hohe Festigkeit, sondern auch eine Vielfalt an Formen und Größen.
Addition statt Subtraktion
Bei herkömmlichen Metallbearbeitungsmethoden wird Abfallmaterial durch maschinelle Bearbeitung entfernt. Der additive Prozess funktioniert umgekehrt – er besteht aus dem Auftragen und Hinzufügen aufeinanderfolgender Schichten kleiner Materialmengen, wodurch XNUMXD-Teile nahezu jeder Form auf der Grundlage eines digitalen Modells erstellt werden.
Obwohl diese Technik sowohl für den Prototypenbau als auch für den Modellguss bereits weit verbreitet ist, war ihre direkte Verwendung bei der Produktion von Waren oder Geräten, die für den Markt bestimmt sind, aufgrund der geringen Effizienz und der unbefriedigenden Materialeigenschaften schwierig. Dank der Arbeit von Forschern in vielen Zentren auf der ganzen Welt ändert sich diese Situation jedoch allmählich.
Durch sorgfältige Experimente wurden die beiden Haupttechnologien des XNUMXD-Drucks verbessert: Laserauftragung von Metall (LMD) und Selektives Laserschmelzen (ULM). Die Lasertechnologie ermöglicht die präzise Erstellung feiner Details und die Erzielung einer guten Oberflächenqualität, was mit dem 50D-Elektronenstrahldruck (EBM) nicht möglich ist. Beim SLM wird die Spitze des Laserstrahls auf das Pulver des Materials gerichtet und verschweißt es lokal nach einem vorgegebenen Muster mit einer Genauigkeit von 250 bis 3 Mikrometern. LMD wiederum verarbeitet das Pulver mithilfe eines Lasers zu selbsttragenden XNUMXD-Strukturen.
Diese Methoden haben sich für die Herstellung von Flugzeugteilen als sehr vielversprechend erwiesen. und insbesondere die Laserabscheidung von Metall erweitert die Designmöglichkeiten für Luft- und Raumfahrtkomponenten. Sie können aus Materialien mit komplexen inneren Strukturen und Verläufen hergestellt werden, die in der Vergangenheit nicht möglich waren. Darüber hinaus ermöglichen beide Lasertechnologien die Herstellung von Produkten mit komplexer Geometrie und die Erzielung einer erweiterten Funktionalität von Produkten aus einer breiten Palette von Legierungen.
Im vergangenen September gab Airbus bekannt, dass es seine Serien-A350 XWB mit additivem Druck ausgestattet hat. Titanhalterung, hergestellt von Arconic. Damit ist aber noch nicht Schluss, denn der Vertrag von Arconic mit Airbus sieht den 3D-Druck aus Titan-Nickel-Pulver vor. Körperteile i Antriebssystem. Es ist jedoch zu beachten, dass Arconic keine Lasertechnologie verwendet, sondern eine eigene verbesserte Version des elektronischen EBM-Lichtbogens.
Einer der Meilensteine in der Entwicklung additiver Technologien in der Metallbearbeitung dürfte der erste Prototyp sein, der im Herbst 2017 am Hauptsitz der niederländischen Damen Shipyards Group vorgestellt wird. Schiffspropeller nach ihr benannte Metalllegierung VAAMpeller. Nach entsprechenden Tests, die größtenteils bereits stattgefunden haben, besteht für das Modell eine Chance auf eine Zulassung für den Einsatz an Bord von Schiffen.
Da die Zukunft der Metallbearbeitungstechnologie in Edelstahlpulvern oder Legierungskomponenten liegt, lohnt es sich, die Hauptakteure in diesem Markt kennenzulernen. Laut dem im November 2017 veröffentlichten „Additive Manufacturing Metal Powder Market Report“ sind die wichtigsten Hersteller von 3D-Druck-Metallpulvern: GKN, Hitachi Chemical, Rio Tinto, ATI Powder Metals, Praxair, Arconic, Sandvik AB, Renishaw, Höganäs AB, Metaldyne Performance Group, BÖHLER Edelstahl, Carpenter Technology Corporation, Aubert & Duval.
Propellerdruck WAAMpeller
Flüssigphase
Die bekanntesten Metalladditivtechnologien basieren derzeit auf der Verwendung von Pulvern (so entsteht der oben erwähnte Vibenit), die bei den für das Ausgangsmaterial erforderlichen hohen Temperaturen „gesintert“ und laserverschmolzen werden. Es entstehen jedoch neue Konzepte. Forscher des Cryobiomedical Engineering Laboratory der Chinesischen Akademie der Wissenschaften in Peking haben eine Methode entwickelt 3D-Druck mit „Tinte“, bestehend aus einer Metalllegierung mit einem Schmelzpunkt etwas über Raumtemperatur. In einer in der Fachzeitschrift Science China Technological Sciences veröffentlichten Studie demonstrieren die Forscher Liu Jing und Wang Lei eine Technik für den Flüssigphasendruck von Legierungen auf Gallium-, Wismut- oder Indiumbasis unter Zusatz von Nanopartikeln.
Im Vergleich zu herkömmlichen Metall-Prototyping-Methoden bietet der Flüssigphasen-3D-Druck mehrere wichtige Vorteile. Erstens kann eine relativ hohe Fertigungsrate dreidimensionaler Strukturen erreicht werden. Darüber hinaus können Sie hier die Temperatur und den Durchfluss des Kühlmittels flexibler einstellen. Darüber hinaus kann flüssiges leitfähiges Metall in Kombination mit nichtmetallischen Materialien (z. B. Kunststoffen) verwendet werden, was die Gestaltungsmöglichkeiten für komplexe Bauteile erhöht.
Wissenschaftler der American Northwestern University haben außerdem eine neue Metall-3D-Drucktechnik entwickelt, die billiger und weniger komplex ist als bisher bekannt. Statt Metallpulver kommen Laser oder Elektronenstrahlen zum Einsatz herkömmlicher Ofen i flüssiges Material. Darüber hinaus funktioniert die Methode gut für eine Vielzahl von Metallen, Legierungen, Verbindungen und Oxiden. Dies ähnelt der Düsendichtung, die wir von Kunststoffen kennen. „Tinte“ besteht aus einem in einer speziellen Substanz gelösten Metallpulver unter Zusatz eines Elastomers. Zum Zeitpunkt der Anwendung hat es Raumtemperatur. Anschließend wird die aus der Düse aufgetragene Materialschicht mit den vorherigen Schichten bei einer im Ofen erzeugten erhöhten Temperatur gesintert. Die Technik wird in der Fachzeitschrift Advanced Functional Materials beschrieben.
Chinesische Flüssigmetallphasendruckmethode
Im Jahr 2016 stellten Harvard-Forscher eine weitere Methode vor, mit der XNUMXD-Metallstrukturen erstellt werden können. gedruckt „in der Luft“. Die Harvard University hat einen 3D-Drucker entwickelt, der im Gegensatz zu anderen Objekten nicht Schicht für Schicht erstellt, sondern komplexe Strukturen „in der Luft“ erzeugt – aus sofort gefrierendem Metall. Das an der John A. Paulson School of Engineering and Applied Sciences entwickelte Gerät druckt Objekte mit Silbernanopartikeln. Der fokussierte Laser erhitzt das Material und verschmilzt es, wodurch verschiedene Strukturen wie etwa eine Helix entstehen.
Die Marktnachfrage nach hochpräzisen 3D-gedruckten Konsumgütern wie medizinischen Implantaten und Flugzeugtriebwerksteilen wächst rasant. Und da Produktdaten mit anderen geteilt werden können, können Unternehmen auf der ganzen Welt, wenn sie Zugang zu Metallpulver und dem richtigen 3D-Drucker haben, daran arbeiten, Logistik- und Lagerkosten zu senken. Wie Sie wissen, erleichtern die beschriebenen Technologien die Herstellung von Metallteilen mit komplexer Geometrie im Vergleich zu herkömmlichen Produktionstechnologien erheblich. Die Entwicklung spezialisierter Anwendungen dürfte zu niedrigeren Preisen und einer Offenheit für den Einsatz des 3D-Drucks auch in herkömmlichen Anwendungen führen.
Der härteste schwedische Stahl – für den 3D-Druck:
Der härteste Stahl der Welt – hergestellt in Uppsala, Schweden
Aluminiumfolie zum Bedrucken:
Durchbruch in der Metallurgie: 3D-Druck von hochfestem Aluminium

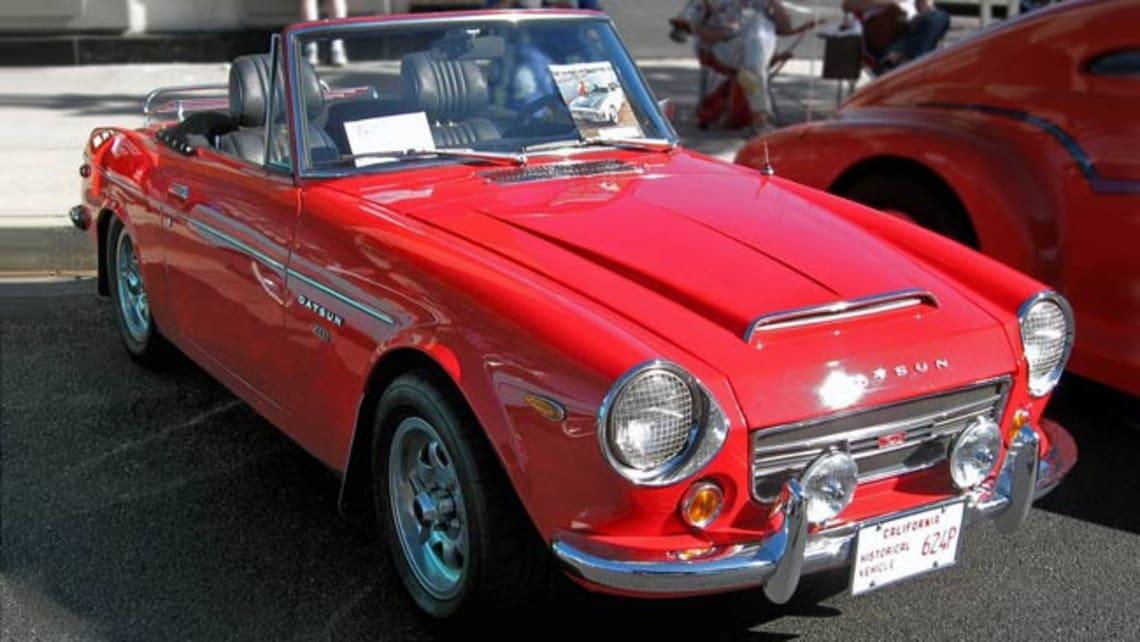
ein Kommentar
anonym
Streich