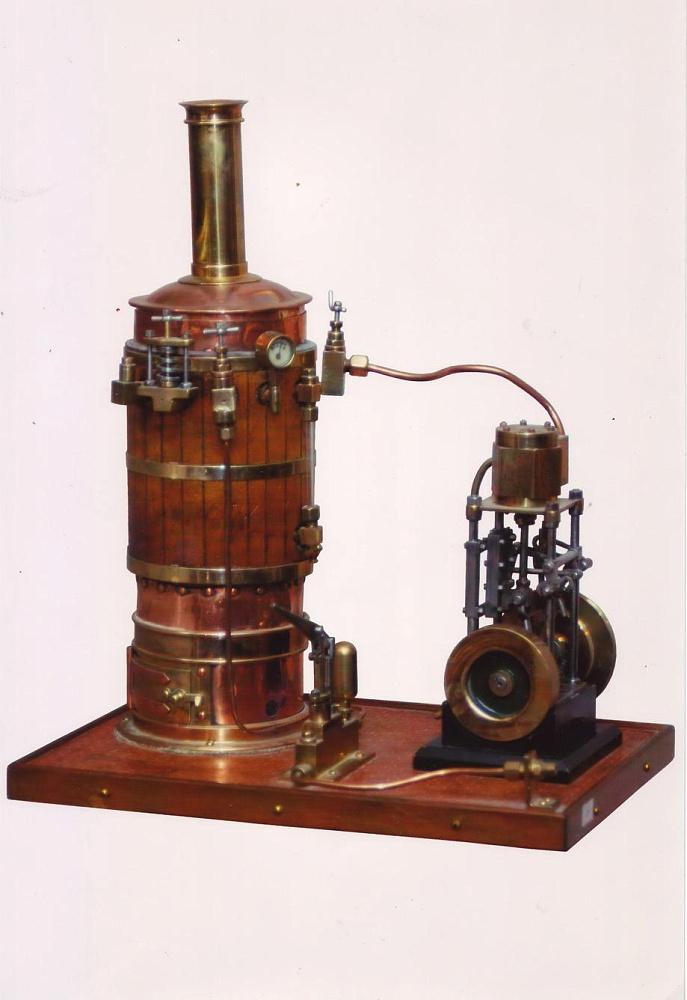
Dampfmaschine aus Holz
Die ersten Dampfmaschinen mit beweglichem Schwingzylinder entstanden im XNUMX. Jahrhundert und dienten dem Antrieb kleiner Dampfschiffe. Zu ihren Vorteilen gehörte die Einfachheit des Designs. Natürlich waren diese Dampfmaschinen nicht aus Holz, sondern aus Metall. Sie bestanden aus wenigen Teilen, gingen nicht kaputt und waren billig in der Herstellung. Sie wurden horizontal oder vertikal hergestellt, sodass sie auf dem Schiff nicht viel Platz einnahmen. Diese Art von Dampfmaschinen wurden auch als funktionierende Miniaturen hergestellt. Dabei handelte es sich um dampfbetriebene polytechnische Spielzeuge.
Die Einfachheit der Konstruktion der Dampfmaschine mit oszillierendem Zylinder ist ihr großer Vorteil, und wir könnten versucht sein, ein solches Modell aus Holz herzustellen. Wir möchten auf jeden Fall, dass unser Modell funktioniert und nicht nur herumsteht. Es ist erreichbar. Allerdings werden wir ihn nicht mit heißem Dampf antreiben, sondern mit normaler kalter Luft, am besten aus einem heimischen Kompressor oder zum Beispiel einem Staubsauger. Holz ist ein interessantes und leicht zu bearbeitendes Material, mit dem sich der Mechanismus einer Dampfmaschine nachbilden lässt. Da wir beim Bau unseres Modells einen seitlich geteilten Teil des Zylinders vorgesehen haben, können wir dank dessen sehen, wie der Kolben funktioniert und wie sich der Zylinder relativ zu den Steuerlöchern bewegt. Ich empfehle Ihnen, sofort mit der Arbeit zu beginnen.
Maschinenbetrieb Dampf mit schwingendem Zylinder. Wir können sie analysieren Foto 1 in einer Fotoserie mit den Bezeichnungen a bis f.
- Durch den Einlass dringt Dampf in den Zylinder ein und drückt den Kolben.
- Der Kolben dreht das Schwungrad über eine Kolbenstange und eine Pleuelkurbel.
- Der Zylinder ändert seine Position; wenn sich der Kolben bewegt, verschließt er den Dampfeinlass und öffnet den Dampfauslass.
- Der Kolben, angetrieben durch die Trägheit des beschleunigenden Schwungrads, drückt den Abgasdampf durch dieses Loch und der Zyklus beginnt von neuem.
- Der Zylinder ändert seine Position und die Einlassöffnung öffnet sich.
- Der komprimierte Dampf strömt erneut durch den Einlass und drückt den Kolben.
Werkzeuge: elektrische Bohrmaschine auf einem Ständer, Bohrmaschine an einer Werkbank befestigt, Bandschleifer, Vibrationsschleifer, Dremel mit Holzbearbeitungsbohrern, Stichsäge, Lötkolben mit Heißkleber, M3-Matrize mit Gewindehalter, Tischlerbohrer 14 Millimeter. Zum Antrieb des Modells nutzen wir einen Kompressor oder einen Staubsauger.
Material: Kiefernbrett 100 mal 20 Millimeter breit, Walze mit einem Durchmesser von 14 Millimetern, Brett 20 mal 20 Millimeter, Brett 30 mal 30 Millimeter, Brett 60 mal 8 Millimeter, Sperrholz 10 Millimeter dick. Silikonfett oder Maschinenöl, ein Nagel mit einem Durchmesser von 3 Millimetern und einer Länge von 60 Millimetern, eine starke Feder, eine Mutter mit einer M3-Unterlegscheibe. Transparenter Lack in einer Aerosoldose zum Lackieren von Holz.
Maschinenbasis. Wir werden es aus einem Brett mit den Maßen 500 x 100 x 20 Millimeter herstellen. Vor dem Lackieren empfiehlt es sich, alle Unebenheiten der Platte und die nach dem Schneiden verbleibenden Stellen mit Schleifpapier auszugleichen.
Schwungradunterstützung. Schneiden wir es aus einem Kiefernbrett mit den Maßen 150 x 100 x 20 Millimeter. Wir benötigen zwei identische Elemente. Nach dem Abrunden mit einem Bandschleifer, Schleifpapier der Körnung 40 entlang der Oberkanten in den Bögen und Feinschleifpapier in den Stützen bohren Sie an den Stellen Löcher mit einem Durchmesser von 14 Millimetern, wie in Abb. Foto 2. Die Höhe des Tretlagers zwischen Basis und Achse muss größer sein als der Radius des Schwungrads.
Schwungradfelge. Wir werden es aus 10 Millimeter dickem Sperrholz schneiden. Das Rad hat einen Durchmesser von 180 Millimetern. Zeichnen Sie mit einem Messschieber zwei identische Kreise auf das Sperrholz und schneiden Sie sie mit einer Stichsäge aus. Zeichnen Sie auf dem ersten Kreis koaxial einen Kreis mit einem Durchmesser von 130 Millimetern und schneiden Sie dessen Mittelpunkt aus. Dies wird der Rand des Schwungrads sein, also sein Rand. Ein Kranz zur Erhöhung der Trägheit eines rotierenden Rades.
Schwungrad. Unser Schwungrad hat fünf Speichen. Sie werden so erstellt, dass wir fünf Dreiecke mit abgerundeten Kanten und einer Drehung um 72 Grad relativ zur Radachse auf das Rad zeichnen. Beginnen wir damit, einen Kreis mit einem Durchmesser von 120 Millimetern auf Papier zu zeichnen, gefolgt von Stricknadeln mit einer Dicke von 15 Millimetern und Kreisen an den Ecken der resultierenden Dreiecke. Sie können es unter sehen Foto 3. i 4., wo das Raddesign gezeigt wird. Legen Sie das Papier auf die ausgeschnittenen Kreise und markieren Sie mit einem Locher die Mittelpunkte aller kleinen Kreise. Dadurch wird die Bohrgenauigkeit gewährleistet. Wir bohren alle Ecken der Dreiecke mit einem Bohrer mit einem Durchmesser von 14 Millimetern. Da ein Paddelbohrer das Sperrholz zerstören kann, empfiehlt es sich, nur durch die halbe Dicke des Sperrholzes zu bohren, das Material dann umzudrehen und den Bohrvorgang abzuschließen. Ein Flachbohrer mit diesem Durchmesser endet in einem winzigen hervorstehenden Stab, der es uns ermöglicht, die Mitte des Bohrlochs auf der anderen Seite des Sperrholzes genau zu lokalisieren. In Anbetracht der Überlegenheit zylindrischer Zimmermannsbohrer gegenüber flachen Zimmermannsbohrern werden wir mit einer Stichsäge das restliche unnötige Material vom Schwungrad abschneiden, um effektive Speichen zu erhalten. Um etwaige Ungenauigkeiten auszugleichen und die Kanten der Stricknadeln abzurunden, verwenden wir einen Dremel. Kleben Sie den Kreis mit dem Kranz mit Vicola-Kleber fest. Wir bohren in der Mitte ein Loch mit einem Durchmesser von 6 Millimetern, um in der Mitte eine M6-Schraube einzuführen und so die ungefähre Drehachse des Rades zu erhalten. Nach dem Einbau des Bolzens als Radachse in die Bohrmaschine bearbeiten wir das schnell rotierende Rad zunächst mit grobkörnigem Schleifpapier und dann mit feinem Schleifpapier. Ich rate Ihnen, die Drehrichtung der Bohrmaschine zu ändern, damit sich die Radschraube nicht löst. Das Rad sollte glatte Kanten haben und sich nach der Bearbeitung gleichmäßig drehen, ohne an die Seite zu stoßen. Wenn dies erreicht ist, demontieren wir den provisorischen Bolzen und bohren ein Loch für die Zielachse mit einem Durchmesser von 14 Millimetern.
Pleuelstange. Wir werden es aus 10 Millimeter dickem Sperrholz schneiden. Um die Arbeit zu erleichtern, empfehle ich, zunächst zwei Löcher mit einem Durchmesser von 14 Millimetern im Abstand von 38 Millimetern zu bohren und erst dann die endgültige klassische Form auszuschneiden, wie in gezeigt Foto 5.
Hier ist das Schwungrad. Es besteht aus einem Schaft mit einem Durchmesser von 14 Millimetern und einer Länge von 190 Millimetern.
Hier ist die Pleuelstange. Es wird aus einem Schaft mit einem Durchmesser von 14 Millimetern und einer Länge von 80 Millimetern geschnitten.
Zylinder. Wir werden es aus 10 Millimeter dickem Sperrholz schneiden. Es besteht aus fünf Elementen. Zwei davon sind 140 mal 60 Millimeter groß und bilden die Seitenwände des Zylinders. Unten und oben 140 mal 80 Millimeter. Der untere Teil des Zylinders misst 60 x 60 und ist 15 Millimeter dick. Diese Teile sind in abgebildet Foto 6. Kleben Sie den Boden und die Seiten des Zylinders mit geflochtenem Kleber fest. Eine der Voraussetzungen für den korrekten Betrieb des Modells ist die Rechtwinkligkeit der Verklebung von Wänden und Boden. Bohren Sie Löcher für Schrauben oben in die Zylinderabdeckung. Wir bohren Löcher mit einem 3-mm-Bohrer so, dass sie in die Mitte der Zylinderwandstärke fallen. Bohren Sie mit einem 8-mm-Bohrer kleine Löcher in die Abdeckung, damit sich die Schraubenköpfe verstecken können.
Der Kolben. Seine Abmessungen betragen 60 mal 60 mal 30 Millimeter. In den Kolben bohren wir ein zentrales Sackloch mit einem Durchmesser von 14 Millimetern und einer Tiefe von 20 Millimetern. Wir werden die Kolbenstange hineinstecken.
Kolbenstange. Es besteht aus einem Schaft mit einem Durchmesser von 14 Millimetern und einer Länge von 320 Millimetern. Die Kolbenstange endet auf der einen Seite mit einem Kolben und auf der anderen Seite mit einem Haken an der Achse der Pleuelkurbel.
Pleuelachsenstange. Wir werden es aus einem Block mit einem Querschnitt von 30 x 30 und einer Länge von 40 Millimetern herstellen. Wir bohren ein 14-mm-Loch in den Block und ein zweites Sackloch senkrecht dazu. In dieses Loch kleben wir das andere freie Ende der Kolbenstange. Reinigen Sie die Innenseite des Durchgangslochs und schleifen Sie es mit feinem, in einer Röhre aufgerolltem Schleifpapier ab. Die Pleuelachse dreht sich im Loch und wir möchten an dieser Stelle die Reibung verringern. Abschließend wird der Griff abgerundet und mit einer Holzfeile oder einem Bandschleifer geschliffen.
Timing-Halterung. Wir werden es aus einem Kiefernbrett schneiden, das 150 x 100 x 20 misst. Nachdem Sie die Stütze geschliffen haben, bohren Sie drei Löcher an den Stellen, wie im Bild gezeigt. Das erste Loch mit einem Durchmesser von 3 mm für die Steuerachse. Die anderen beiden sind der Lufteinlass und -auslass des Zylinders. Der Bohrpunkt für alle drei ist in gezeigt Foto 7. Bei der Änderung der Abmessungen von Maschinenteilen müssen die Bohrstellen experimentell ermittelt werden, indem die Maschine vormontiert und die obere und untere Position des Zylinders, nämlich die Stelle des im Zylinder gebohrten Lochs, ermittelt wird. Die Stelle, an der der Zahnriemen arbeiten soll, wird mit einem Exzenterschleifer mit feinem Papier geschliffen. Es sollte gleichmäßig und sehr glatt sein.
Schwingende Nockenwelle. Stumpfen Sie das Ende eines 60-mm-Nagels ab und runden Sie es mit einer Feile oder einem Schleifer ab. Schneiden Sie das Ende mit einer M3-Matrize auf eine Länge von etwa 10 Millimetern ab. Wählen Sie dazu eine starke Feder, eine M3-Mutter und eine Unterlegscheibe.
Verteilung. Wir werden es aus einem Streifen von 140 x 60 x 8 Millimetern herstellen. In diesen Teil des Modells bohren wir zwei Löcher. Der erste mit einem Durchmesser von 3 Millimetern. Wir werden einen Nagel darin platzieren, der die Drehachse des Zylinders darstellt. Denken Sie daran, das Loch so zu bohren, dass der Nagelkopf vollständig im Holz verankert ist und nicht über die Oberfläche hinausragt. Dies ist ein sehr wichtiger Moment in unserer Arbeit, der sich auf den korrekten Betrieb des Modells auswirkt. Das zweite Loch mit einem Durchmesser von 10 Millimetern ist das Lufteinlass- und -auslassloch. Abhängig von der Position des Zylinders in Bezug auf die Löcher im Steuerträger gelangt Luft unter den Kolben, drückt ihn und wird dann vom Kolben in die entgegengesetzte Richtung herausgedrückt. Das Steuerrad und der als Achse dienende Klebenagel werden auf die Oberfläche des Zylinders geklebt. Die Achse sollte nicht wackeln und senkrecht zur Oberfläche stehen. Zum Schluss bohren wir ein Loch in den Zylinder und orientieren uns dabei an der Position des Lochs im Steuergehäusedeckel. Mit einem Schwingschleifer und feinem Schleifpapier glätten wir alle Unebenheiten des Holzes an der Stelle, an der es mit dem Zahnriemen in Berührung kommt.
Maschinenmontage. Kleben Sie die Schwungradachsträger auf die Basis und achten Sie darauf, dass sie in einer Linie und parallel zur Ebene der Basis liegen. Vor der kompletten Montage lackieren wir die Elemente und Komponenten der Maschine mit Klarlack. Wir platzieren die Pleuelstange auf der Schwungradachse und kleben sie genau senkrecht dazu. Wir stecken die Pleuelachse in das zweite Loch. Beide Achsen müssen parallel zueinander sein. Kleben Sie hölzerne Verstärkungsringe auf das Schwungrad. Führen Sie von der Außenseite des Rings eine Holzschraube in das Loch ein, das das Schwungrad an der Schwungradachse befestigt. Kleben Sie den Zylinderträger auf die andere Seite des Sockels. Schmieren Sie alle Holzteile, die sich bewegen und miteinander in Kontakt kommen, mit Silikonfett oder Maschinenöl. Das Silikon sollte leicht poliert sein, um die Reibung zu minimieren. Davon hängt der ordnungsgemäße Betrieb der Maschine ab. Der Zylinder ist so auf dem Schlitten montiert, dass seine Achse über den Zahnriemen hinausragt. Sie können es unter sehen Foto 8. Auf den über die Stütze hinausragenden Nagel legen wir eine Feder, dann eine Unterlegscheibe und befestigen das Ganze mit einer Mutter. Der von der Feder gedrückte Zylinder sollte sich leicht um seine Achse bewegen. Wir setzen den Kolben an seinen Platz im Zylinder und setzen das Ende der Kolbenstange auf die Pleuelachse. Setzen Sie den Zylinderdeckel auf und befestigen Sie ihn mit Holzschrauben. Alle zusammenwirkenden Teile des Mechanismus, insbesondere Zylinder und Kolben, mit Maschinenöl schmieren. Sparen wir nicht am Fett. Bei Bewegung von Hand sollte sich das Rad ohne nennenswerten Widerstand drehen und die Pleuelstange sollte die Bewegung auf Kolben und Zylinder übertragen. Foto 9. Stecken Sie das Ende des Kompressorschlauchs in den Einlass und schalten Sie ihn ein. Drehen Sie das Rad und die Druckluft bewegt den Kolben und das Schwungrad beginnt sich zu drehen. Der kritische Punkt in unserem Modell ist der Kontakt zwischen der Steuerplatte und ihrem Stator. Wenn auf diesem Weg nicht der Großteil der Luft entweicht, sollte sich eine richtig konstruierte Maschine leicht bewegen lassen und dem Heimwerker viel Spaß bereiten. Die Ursache der Fehlfunktion kann eine zu schwache Feder sein. Nach einiger Zeit zieht das Öl in das Holz ein und die Reibung wird zu groß. Dies erklärt auch, warum die Menschen keine Dampfmaschinen aus Holz gebaut haben. Allerdings ist die Holzmaschine sehr effizient und das Wissen darüber, wie der oszillierende Zylinder in einer so einfachen Dampfmaschine funktioniert, bleibt lange erhalten.
Dampfmaschine aus Holz
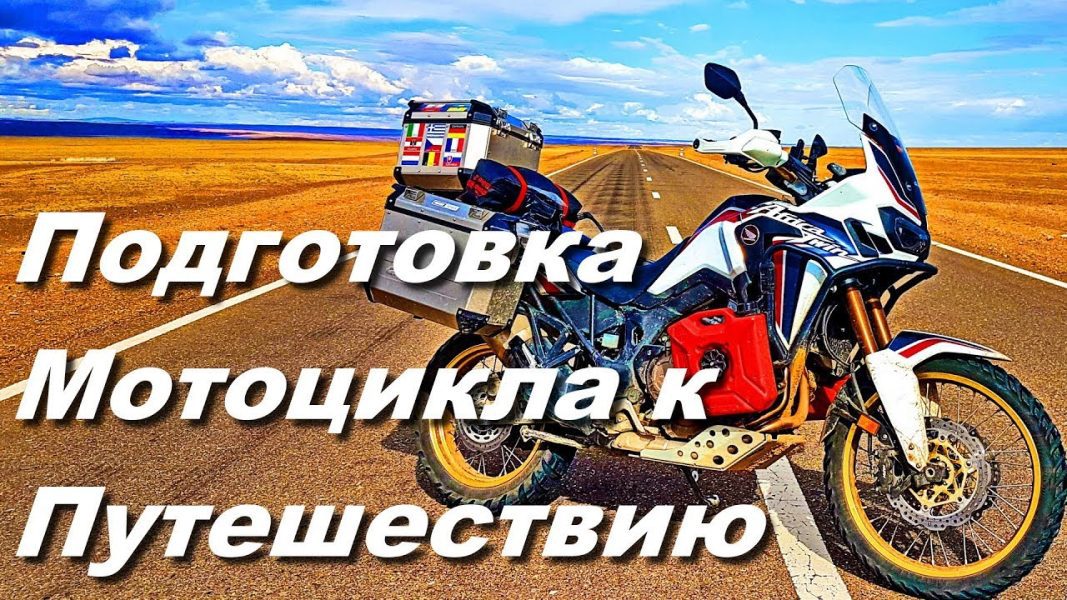
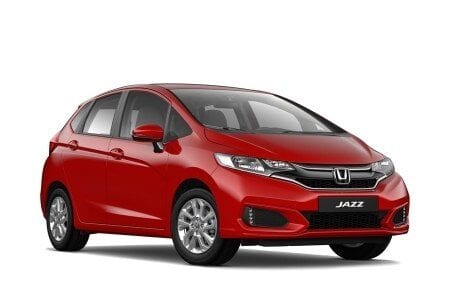