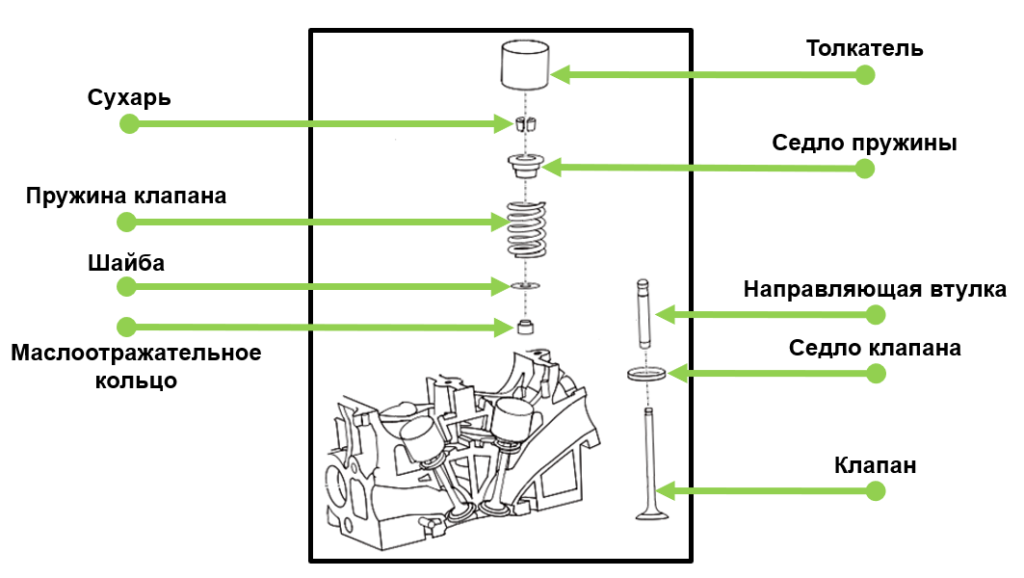
Der Ventilmechanismus des Motors, seine Vorrichtung und sein Funktionsprinzip
Inhalt
Der Ventilmechanismus ist ein direkter Zeitsteuerungsaktuator, der die rechtzeitige Zufuhr des Luft-Kraftstoff-Gemisches zu den Motorzylindern und die anschließende Freisetzung von Abgasen gewährleistet. Kernelemente des Systems sind Ventile, die unter anderem für die Dichtheit des Brennraums sorgen müssen. Da sie hohen Belastungen ausgesetzt sind, gelten für ihre Arbeit besondere Anforderungen.
Die Hauptelemente des Ventilmechanismus
Um ordnungsgemäß zu funktionieren, benötigt der Motor mindestens zwei Ventile pro Zylinder, ein Einlass- und ein Auslassventil. Das Ventil selbst besteht aus einem Schaft und einem Kopf in Form einer Platte. Der Sitz ist die Stelle, an der der Ventilkopf auf den Zylinderkopf trifft. Einlassventile haben einen größeren Kopfdurchmesser als Auslassventile. Dadurch wird eine bessere Füllung des Brennraums mit dem Luft-Kraftstoff-Gemisch gewährleistet.
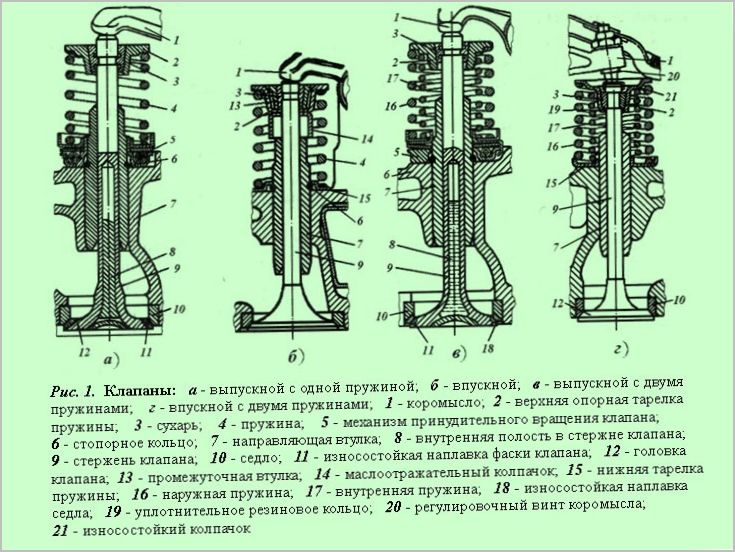
Die Hauptelemente des Mechanismus:
- Einlass- und Auslassventile – für den Eintritt des Luft-Kraftstoff-Gemisches und der Abgase aus der Brennkammer;
- Führungsbuchsen – sorgen für die genaue Bewegungsrichtung der Ventile;
- Feder – bringt das Ventil in seine ursprüngliche Position zurück;
- Ventilsitz – die Kontaktstelle der Platte mit dem Zylinderkopf;
- Cracker – dienen als Stütze für die Feder und fixieren die gesamte Struktur);
- Ventilschaftdichtungen oder Ölschleuderringe – verhindern das Eindringen von Öl in den Zylinder;
- Drücker – überträgt den Druck von der Nockenwelle.
Die Nocken auf der Nockenwelle drücken auf die Ventile, die federbelastet in ihre Ausgangsposition zurückkehren. Die Feder wird mit Crackern und einem Federteller an der Stange befestigt. Um Resonanzschwingungen zu dämpfen, können nicht eine, sondern zwei Federn mit vielseitiger Wicklung an der Stange angebracht werden.
Die Führungshülse ist ein zylindrisches Stück. Es reduziert die Reibung und sorgt für einen reibungslosen und korrekten Betrieb der Rute. Im Betrieb sind diese Teile zudem Belastungen und Temperaturen ausgesetzt. Daher werden für ihre Herstellung verschleißfeste und hitzebeständige Legierungen verwendet. Aufgrund der unterschiedlichen Belastung unterscheiden sich die Buchsen der Auslass- und Einlassventile geringfügig.
Wie der Ventilmechanismus funktioniert
Ventile sind ständig hohen Temperaturen und Drücken ausgesetzt. Dies erfordert besondere Aufmerksamkeit für das Design und die Materialien dieser Teile. Dies gilt insbesondere für die Abgasgruppe, da durch sie heiße Gase austreten. Die Auslassventilplatte kann bei Benzinmotoren auf 800 °C bis 900 °C und bei Dieselmotoren auf 500 °C bis 700 °C erhitzt werden. Die Belastung der Einlassventilplatte ist um ein Vielfaches geringer, erreicht aber 300 °C, was ebenfalls ziemlich viel ist.
Daher werden bei ihrer Herstellung hitzebeständige Metalllegierungen mit Legierungszusätzen verwendet. Darüber hinaus verfügen Auslassventile typischerweise über einen mit Natrium gefüllten Hohlschaft. Dies ist für eine bessere Thermoregulierung und Kühlung der Platte notwendig. Das Natrium im Inneren des Stabes schmilzt, fließt, nimmt einen Teil der Wärme von der Platte auf und überträgt sie auf den Stab. Auf diese Weise kann eine Überhitzung des Teils vermieden werden.
Während des Betriebs kann es zu Kohlenstoffablagerungen am Sattel kommen. Um dies zu verhindern, werden Konstruktionen zum Drehen des Ventils verwendet. Der Sitz ist ein hochfester Stahllegierungsring, der für einen engeren Kontakt direkt in den Zylinderkopf gepresst wird.
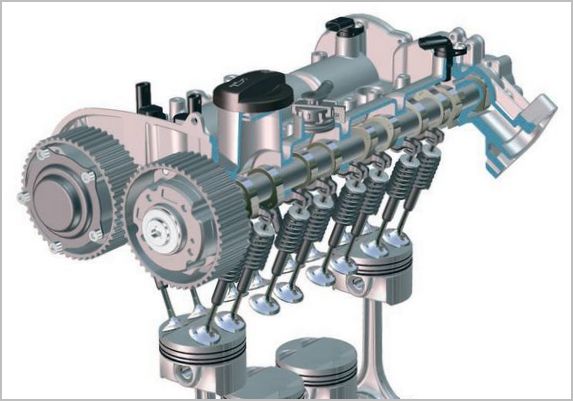
Darüber hinaus ist es für den ordnungsgemäßen Betrieb des Mechanismus erforderlich, den regulierten thermischen Abstand einzuhalten. Durch hohe Temperaturen dehnen sich Teile aus, was zu Fehlfunktionen des Ventils führen kann. Der Spalt zwischen den Nockenwellennocken und den Drückern wird durch Auswahl spezieller Metallscheiben einer bestimmten Dicke oder der Drücker selbst (Gläser) eingestellt. Wenn der Motor Hydrostößel verwendet, wird der Spalt automatisch angepasst.
Ein sehr großer Spielspalt verhindert, dass sich das Ventil vollständig öffnet, und daher füllen sich die Zylinder weniger effizient mit frischem Gemisch. Ein kleiner Spalt (oder das Fehlen eines Spalts) verhindert ein vollständiges Schließen der Ventile, was zum Durchbrennen der Ventile und zu einer Verringerung der Motorkompression führt.
Klassifizierung nach Anzahl der Ventile
Die klassische Version des Viertaktmotors benötigt zum Betrieb nur zwei Ventile pro Zylinder. Da moderne Motoren jedoch immer höhere Anforderungen an Leistung, Kraftstoffverbrauch und Umweltschutz stellen, reicht ihnen das nicht mehr aus. Denn je mehr Ventile vorhanden sind, desto effizienter ist es, den Zylinder mit einer neuen Ladung zu füllen. Zu verschiedenen Zeitpunkten wurden die folgenden Schemata an Motoren getestet:
- Dreiventil (Einlass - 2, Auslass - 1);
- Vierventiler (Einlass – 2, Auslass – 2);
- Fünfventiler (Einlass - 3, Auslass - 2).
Eine bessere Befüllung und Reinigung der Flaschen wird durch mehr Ventile pro Flasche erreicht. Dies erschwert jedoch die Konstruktion des Motors.
Heute am beliebtesten sind Motoren mit 4 Ventilen pro Zylinder. Der erste dieser Motoren erschien 1912 beim Peugeot Gran Prix. Zu dieser Zeit war diese Lösung noch nicht weit verbreitet, aber seit 1970 begann die aktive Produktion von Massenautos mit einer solchen Anzahl von Ventilen.
Antriebsdesign
Für den korrekten und rechtzeitigen Betrieb des Ventilmechanismus sind Nockenwelle und Steuertrieb verantwortlich. Das Design und die Anzahl der Nockenwellen für jeden Motortyp werden individuell ausgewählt. Ein Teil ist eine Welle, auf der sich Nocken einer bestimmten Form befinden. Beim Drehen üben sie Druck auf die Stößel, Hydrostößel oder Kipphebel aus und öffnen die Ventile. Die Art der Schaltung hängt vom jeweiligen Motor ab.
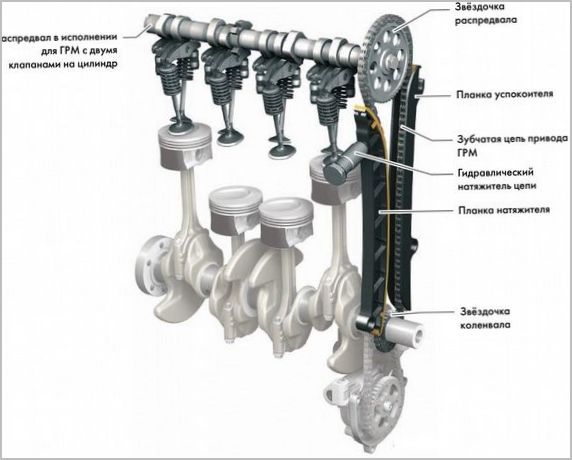
Die Nockenwelle sitzt direkt im Zylinderkopf. Der Antrieb erfolgt über die Kurbelwelle. Es kann eine Kette, ein Riemen oder ein Zahnrad sein. Am zuverlässigsten ist die Kette, sie erfordert jedoch Hilfsgeräte. Zum Beispiel ein Kettenschwingungsdämpfer (Dämpfer) und ein Spanner. Die Drehzahl der Nockenwelle ist halb so groß wie die Drehzahl der Kurbelwelle. Dies stellt ihre koordinierte Arbeit sicher.
Die Anzahl der Nockenwellen hängt von der Anzahl der Ventile ab. Es gibt zwei Hauptschemata:
- SOHC – mit einem Schaft;
- DOHC – zwei Wellen.
Für eine Nockenwelle reichen nur zwei Ventile. Es dreht sich und öffnet abwechselnd die Einlass- und Auslassventile. Die gängigsten Vierventilmotoren verfügen über zwei Nockenwellen. Einer garantiert die Funktion der Einlassventile und der andere die Funktion der Auslassventile. V-Motoren sind mit vier Nockenwellen ausgestattet. Zwei auf jeder Seite.
Die Nockenwellennocken drücken nicht direkt auf den Ventilschaft. Es gibt verschiedene Arten von „Vermittlern“:
- Rollenhebel (Kipphebel);
- mechanische Drücker (Brillen);
- hydraulische Drücker.
Rollenhebel sind die bevorzugte Anordnung. Die sogenannten Kipphebel schwingen auf Steckachsen und üben Druck auf den hydraulischen Drücker aus. Um die Reibung zu verringern, ist am Hebel eine Rolle vorgesehen, die direkten Kontakt mit der Nocke herstellt.
In einem anderen Schema werden hydraulische Drücker (Spaltkompensatoren) verwendet, die direkt an der Stange angebracht sind. Hydraulische Kompensatoren passen den thermischen Spalt automatisch an und sorgen für einen gleichmäßigeren und leiseren Betrieb des Mechanismus. Dieses kleine Teil besteht aus einem Zylinder mit Kolben und Feder, Ölkanälen und einem Rückschlagventil. Der hydraulische Schieber wird mit Öl angetrieben, das vom Motorschmiersystem geliefert wird.
Mechanische Drücker (Gläser) sind einseitig geschlossene Buchsen. Sie werden im Zylinderkopfgehäuse eingebaut und übertragen die Kraft direkt auf den Ventilschaft. Seine Hauptnachteile sind die Notwendigkeit, die Lücken und Schläge beim Arbeiten mit kaltem Motor regelmäßig anzupassen.
Lärm am Arbeitsplatz
Die Fehlfunktion des Hauptventils ist ein Klopfen an einem kalten oder heißen Motor. Das Klopfen bei kaltem Motor verschwindet, wenn die Temperatur steigt. Wenn sie sich erwärmen und ausdehnen, schließt sich die thermische Lücke. Darüber hinaus kann die Viskosität des Öls, das nicht in der richtigen Menge in die Hydrostößel fließt, die Ursache sein. Auch eine Verschmutzung der Ölkanäle des Kompensators kann Ursache für das charakteristische Klopfen sein.
Ventile können bei einem heißen Motor aufgrund eines niedrigen Öldrucks im Schmiersystem, eines verschmutzten Ölfilters oder eines falschen thermischen Spiels klopfen. Es ist auch notwendig, den natürlichen Verschleiß der Teile zu berücksichtigen. Fehler können im Ventilmechanismus selbst liegen (Verschleiß der Feder, Führungshülse, Hydrostößel usw.).
Lückenanpassung
Einstellungen werden nur bei kaltem Motor vorgenommen. Die aktuelle thermische Lücke wird durch spezielle flache Metallsonden unterschiedlicher Dicke ermittelt. Um den Spalt an den Kipphebeln zu verändern, gibt es eine spezielle Einstellschraube, die sich dreht. Bei Systemen mit Drücker oder Unterlegscheiben erfolgt die Anpassung durch Auswahl von Teilen mit der erforderlichen Dicke.
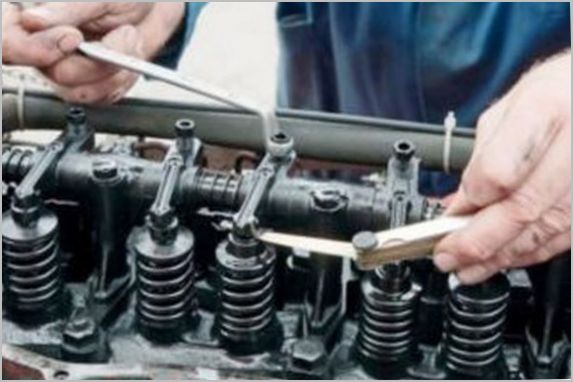
Betrachten Sie den schrittweisen Prozess zum Einstellen von Ventilen für Motoren mit Drückern (Gläsern) oder Unterlegscheiben:
- Entfernen Sie die Motorventilabdeckung.
- Drehen Sie die Kurbelwelle so, dass sich der Kolben des ersten Zylinders im oberen Totpunkt befindet. Wenn dies aufgrund von Markierungen schwierig ist, können Sie die Zündkerze abschrauben und einen Schraubendreher in das Loch einführen. Seine maximale Aufwärtsbewegung wird im Totpunkt sein.
- Messen Sie mit einem Satz Fühlerlehren das Ventilspiel unter den Nocken, die nicht auf die Stößel drücken. Die Sonde sollte ein knappes, aber nicht zu freies Spiel haben. Notieren Sie die Ventilnummer und den Spielwert.
- Drehen Sie die Kurbelwelle um eine Umdrehung (360°), um den Kolben des 4. Zylinders auf den oberen Totpunkt zu bringen. Messen Sie den Abstand unter den übrigen Ventilen. Notieren Sie die Daten.
- Prüfen Sie, welche Ventile außerhalb der Toleranz liegen. Falls vorhanden, wählen Sie Drücker mit der gewünschten Dicke aus, entfernen Sie die Nockenwellen und setzen Sie neue Gläser ein. Damit ist der Vorgang abgeschlossen.
Es wird empfohlen, die Lücken alle 50-80 Kilometer zu überprüfen. Standardwerte für das Spiel finden Sie im Reparaturhandbuch des Fahrzeugs.
Bitte beachten Sie, dass das Einlass- und Auslassventilspiel manchmal unterschiedlich sein kann.
Ein richtig eingestellter und abgestimmter Gasverteilungsmechanismus gewährleistet einen reibungslosen und gleichmäßigen Betrieb des Verbrennungsmotors. Dies wird sich auch positiv auf die Motorressourcen und den Fahrerkomfort auswirken.
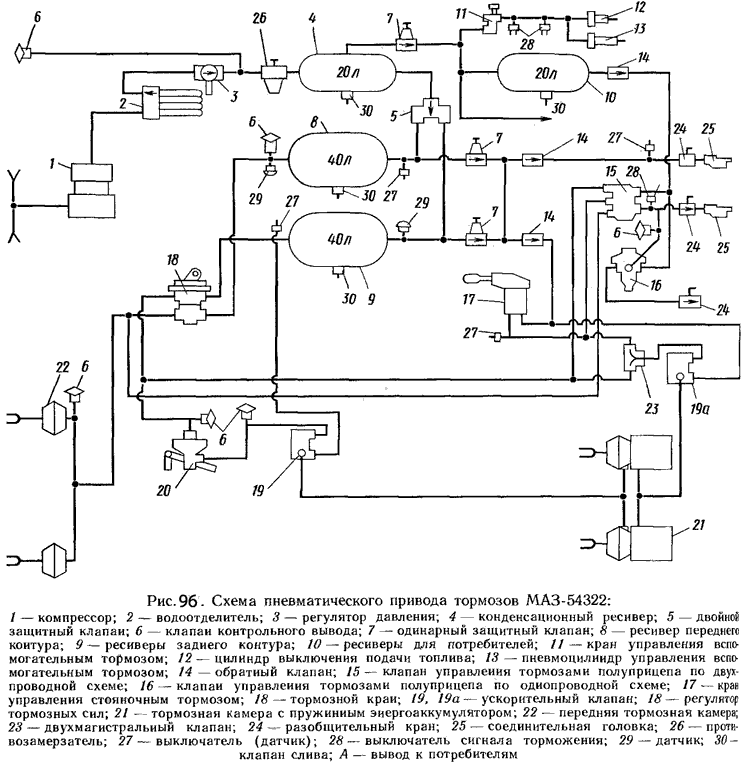
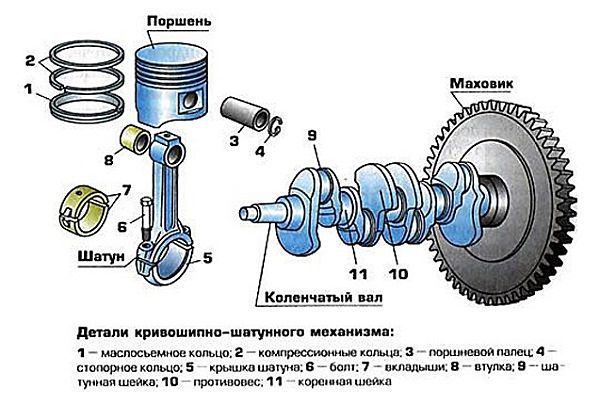