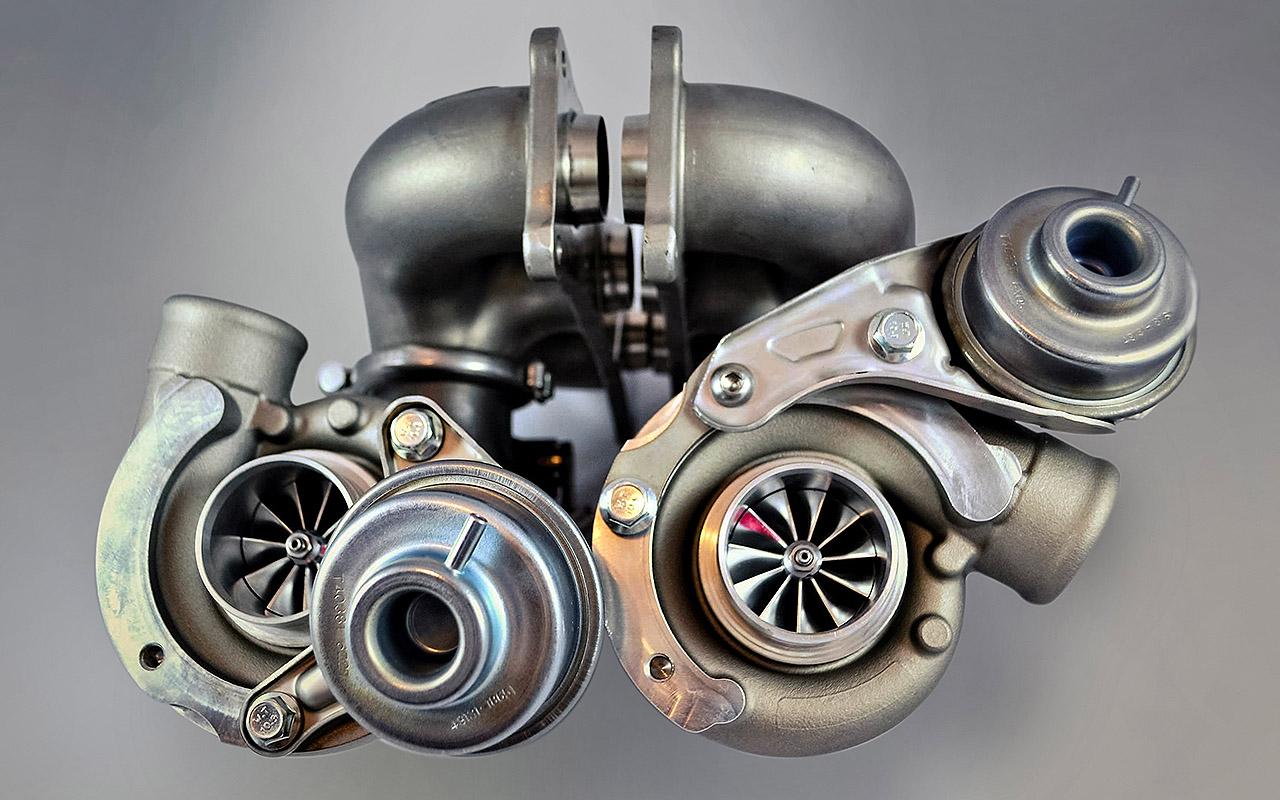
Die Ermäßigung. Turbo in einem kleinen Motor. Die ganze Wahrheit über moderne Technologie
Inhalt
Mittlerweile ist es für Hersteller fast Standard, leistungsschwache Antriebsstränge in Autos einzubauen, selbst in Autos wie den Volkswagen Passat oder den Skoda Superb. Die Idee der Reduzierung hat sich zum Besseren entwickelt und die Zeit hat gezeigt, dass diese Lösung jeden Tag funktioniert. Ein wichtiges Element bei diesem Motortyp ist natürlich der Turbolader, mit dem man relativ viel Leistung bei gleichzeitig geringer Leistung erzielen kann.
Wirkprinzip
Der Turbolader besteht aus zwei gleichzeitig rotierenden Rotoren, die auf einer gemeinsamen Welle montiert sind. Der erste wird in die Abgasanlage eingebaut, die Abgase sorgen für Bewegung, gelangen in die Schalldämpfer und werden herausgeschleudert. Der zweite Rotor befindet sich im Ansaugsystem, komprimiert die Luft und beaufschlagt sie mit Druck in den Motor.
Dieser Druck muss kontrolliert werden, damit nicht zu viel davon in die Brennkammer gelangt. Einfache Systeme verwenden die Form eines Bypassventils, während fortgeschrittene Designs, d. h. Am häufigsten werden Klingen mit variabler Geometrie verwendet.
Siehe auch: Top 10 Möglichkeiten zur Reduzierung des Kraftstoffverbrauchs
Leider ist die Luft im Moment der hohen Kompression sehr heiß, außerdem wird sie durch das Turboladergehäuse erhitzt, was wiederum ihre Dichte verringert, was sich negativ auf die ordnungsgemäße Verbrennung des Kraftstoff-Luft-Gemisches auswirkt. Daher verwenden Hersteller beispielsweise einen Ladeluftkühler, dessen Aufgabe es ist, die erhitzte Luft abzukühlen, bevor sie in den Brennraum gelangt. Beim Abkühlen wird es dicker, wodurch mehr davon in den Zylinder gelangen kann.
Kompressor und Turbolader von Eaton
Bei einem Motor mit zwei Ladern, einem Turbolader und einem mechanischen Kompressor sind diese auf beiden Seiten des Motors verbaut. Dies liegt daran, dass es sich bei der Turbine um einen Hochtemperaturgenerator handelt. Die optimale Lösung besteht daher darin, auf der gegenüberliegenden Seite einen mechanischen Kompressor zu installieren. Der Eaton-Kompressor unterstützt den Betrieb des Turboladers und wird über einen Keilrippenriemen von der Hauptriemenscheibe der Wasserpumpe angetrieben, die mit einer wartungsfreien elektromagnetischen Kupplung ausgestattet ist, die für ihre Aktivierung verantwortlich ist.
Durch entsprechende innere Proportionen und die Übersetzung des Riemenantriebs drehen sich die Kompressorrotoren mit der fünffachen Geschwindigkeit der Kurbelwelle eines Pkw-Antriebs. Der Kompressor ist saugrohrseitig am Motorblock befestigt und die Regeldrossel dosiert den erzeugten Druck.
Bei geschlossener Drosselklappe erzeugt der Kompressor den maximalen Druck für die aktuelle Geschwindigkeit. Anschließend wird komprimierte Luft in den Turbolader gedrückt und bei zu hohem Druck öffnet sich die Drosselklappe, wodurch die Luft in den Kompressor und den Turbolader aufgeteilt wird.
Schwierigkeiten bei der Arbeit
Die oben erwähnte hohe Betriebstemperatur und die wechselnden Belastungen der Strukturelemente sind Faktoren, die sich hauptsächlich negativ auf die Lebensdauer des Turboladers auswirken. Unsachgemäßer Betrieb führt zu schnellerem Verschleiß des Mechanismus, Überhitzung und in der Folge zum Ausfall. Es gibt mehrere verräterische Symptome einer Turboladerstörung, wie etwa ein lauteres „Pfeifen“, plötzlicher Leistungsverlust beim Beschleunigen, blauer Rauch aus dem Auspuff, Übergang in den Notlaufmodus und eine Motorfehlermeldung namens „Bump“. „Motor prüfen“ und auch rund um die Turbine und im Luftansaugrohr mit Öl schmieren.
Einige moderne Kleinmotoren verfügen über eine Lösung, um den Turbo vor Überhitzung zu schützen. Um einen Wärmestau zu vermeiden, ist die Turbine mit Kühlmittelkanälen ausgestattet, was bedeutet, dass bei ausgeschaltetem Motor die Flüssigkeit weiter fließt und der Prozess fortgesetzt wird, bis die entsprechende Temperatur entsprechend den thermischen Eigenschaften erreicht ist. Möglich macht dies eine elektrische Kühlmittelpumpe, die unabhängig vom Verbrennungsmotor arbeitet. Die Motorsteuerung (über ein Relais) regelt ihren Betrieb und aktiviert ihn, wenn der Motor ein Drehmoment von mehr als 100 Nm erreicht und die Lufttemperatur im Ansaugkrümmer mehr als 50 °C beträgt.
Turbo-Loch-Effekt
Der Nachteil einiger aufgeladener Motoren mit höherer Leistung ist der sog. Turboloch-Effekt, d.h. eine vorübergehende Abnahme der Motoreffizienz zum Zeitpunkt des Starts oder der Wunsch, stark zu beschleunigen. Je größer der Kompressor, desto deutlicher wird der Effekt, da er mehr Zeit für das sogenannte „Spinning“ benötigt.
Ein kleiner Motor entwickelt seine Leistung kräftiger, die verbaute Turbine ist relativ klein, so dass der beschriebene Effekt minimiert wird. Das Drehmoment steht bereits bei niedrigen Motordrehzahlen zur Verfügung, was einen komfortablen Betrieb beispielsweise im Stadtverkehr gewährleistet. Zum Beispiel in einem VW 1.4 TSI-Motor mit 122 PS. (EA111) stehen bereits bei 1250 U/min etwa 80 % des Gesamtdrehmoments zur Verfügung, der maximale Ladedruck beträgt 1,8 bar.
Um das Problem vollständig zu lösen, entwickelten Ingenieure eine relativ neue Lösung, nämlich einen elektrischen Turbolader (E-Turbo). Dieses System kommt zunehmend bei Motoren mit geringer Leistung zum Einsatz. Die Methode basiert darauf, dass der Rotor, der die in den Motor eingespritzte Luft antreibt, mit Hilfe eines Elektromotors rotiert – dadurch kann der Effekt praktisch eliminiert werden.
Wahr oder Mythos?
Viele Menschen befürchten, dass Turbolader in unterdimensionierten Motoren schneller ausfallen können, was möglicherweise an der Tatsache liegt, dass sie überlastet sind. Leider ist dies ein häufig wiederholter Mythos. Die Wahrheit ist, dass die Langlebigkeit stark davon abhängt, wie Sie Ihr Öl verwenden, fahren und wechseln – etwa 90 % des Schadens werden vom Benutzer verursacht.
Es wird davon ausgegangen, dass Autos mit einer Laufleistung von 150-200 km zur Gruppe mit erhöhtem Ausfallrisiko gehören. In der Praxis haben viele Autos mehr als einen Kilometer zurückgelegt und das beschriebene Aggregat funktioniert bis heute einwandfrei. Mechaniker behaupten, dass ein Ölwechsel alle 30-10 Kilometer, d.h. Lange Lebensdauer wirkt sich negativ auf den Zustand des Turboladers und des Motors selbst aus. Deshalb werden wir die Austauschintervalle auf 15 verkürzen. km und verwenden Sie das Öl gemäß den Empfehlungen Ihres Fahrzeugherstellers und Sie können sich lange an einem störungsfreien Betrieb erfreuen.
Mögliche Regenerierung der Elementkosten von 900 PLN bis 2000 PLN. Ein neuer Turbo kostet viel mehr - sogar mehr als 4000 zł.
Siehe auch: Fiat 500C in unserem Test
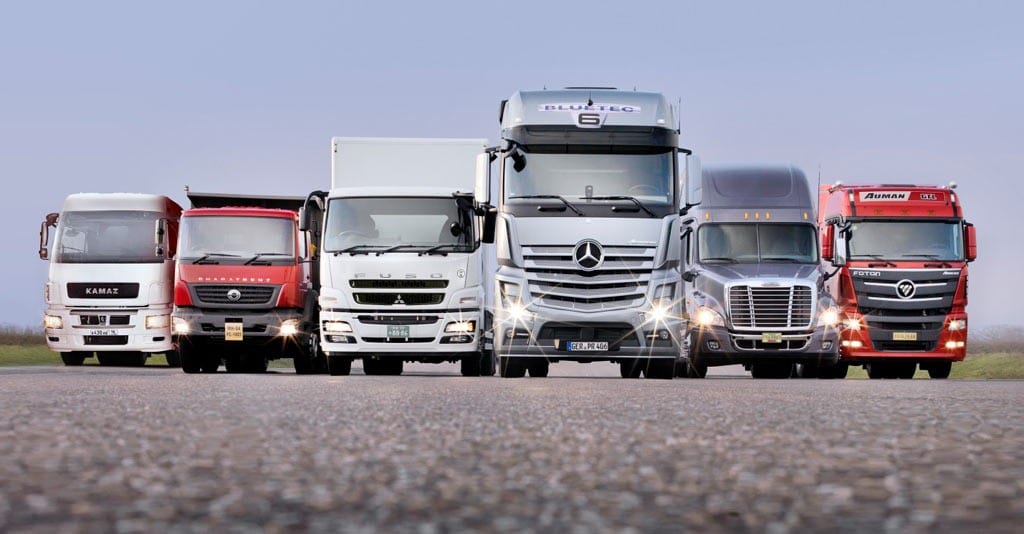
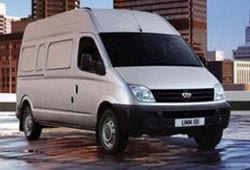