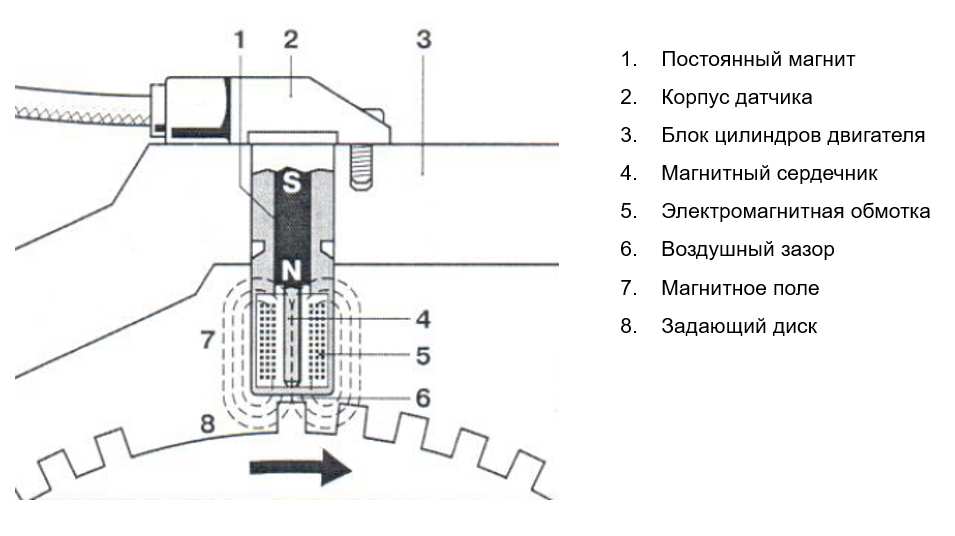
Kurbelwellenpositionssensor
Inhalt
Der Kurbelwellensensor steuert von der Motor-ECU die Position des mechanischen Teils, das für den Betrieb des Kraftstoffeinspritzsystems verantwortlich ist. Wenn das DPKV ausfällt, wird es mit Hilfe spezieller Tester diagnostiziert, die nach dem Prinzip eines Ohmmeters arbeiten. Falls der aktuelle Widerstandswert unter dem Nennwert liegt, ist ein Reglertausch erforderlich.
Wofür ist der Kurbelwellensensor verantwortlich und wie funktioniert er?
Der Kurbelwellenpositionssensor bestimmt genau, wann Kraftstoff zu den Zylindern des Verbrennungsmotors (ICE) geleitet werden sollte. Das DPKV übernimmt in unterschiedlichen Ausführungen die Steuerung der Einstellung der Gleichmäßigkeit der Kraftstoffzufuhr durch die Injektoren.
Die Funktionen des Kurbelwellensensors bestehen darin, folgende Daten zu erfassen und an den Computer zu übertragen:
- die Position der Kurbelwelle messen;
- in dem Moment, in dem die Kolben im ersten und letzten Zylinder UT und OT passieren.
Der PKV-Sensor korrigiert die folgenden Anzeigen:
- die Menge des ankommenden Kraftstoffs;
- Zeitpunkt der Benzinzufuhr;
- Nockenwellenwinkel;
- Zündzeitpunkt;
- Moment und Dauer des Betriebs des Adsorptionsventils.
Das Funktionsprinzip des Zeitsensors:
- Die Kurbelwelle ist mit einer Scheibe mit Zähnen ausgestattet (Starten und Nullstellen). Wenn sich die Baugruppe dreht, wird das Magnetfeld vom PKV-Sensor auf die Zähne gerichtet und wirkt darauf ein. Änderungen werden in Form von Impulsen erfasst und an den Computer übermittelt: Die Position der Kurbelwelle wird gemessen und der Moment erfasst, in dem die Kolben den oberen und unteren Totpunkt (OT und UT) passieren.
- Wenn das Kettenrad den Kurbelwellendrehzahlsensor passiert, ändert es die Art der Ladedruckanzeige. Aus diesem Grund versucht die ECU, den normalen Betrieb der Kurbelwelle wiederherzustellen.
- Basierend auf den empfangenen Impulsen sendet der Bordcomputer ein Signal an die erforderlichen Fahrzeugsysteme.
DPKV-Gerät
Aufbau des Kurbelwellensensors:
- ein zylindrisches Aluminium- oder Kunststoffgehäuse mit einem empfindlichen Element, durch das ein Signal an den Computer gesendet wird;
- Kommunikationskabel (Magnetkreis);
- Antriebseinheit;
- Dichtungsmittel;
- Wicklung;
- Motorhalterung.
Tabelle: Arten von Sensoren
Name | Beschreibung |
Magnetsensor | Der Sensor besteht aus einem Permanentmagneten und einer zentralen Wicklung, und diese Art der Steuerung benötigt keine separate Stromversorgung. Ein induktives elektrisches Gerät steuert nicht nur die Position der Kurbelwelle, sondern auch die Drehzahl. Es arbeitet mit der Spannung, die entsteht, wenn ein Metallzahn (Tag) ein Magnetfeld durchläuft. Dadurch wird ein Signalimpuls erzeugt, der an die ECU geht. |
Optischer Sensor | Der optische Sensor besteht aus einem Empfänger und einer LED. In Wechselwirkung mit der Taktscheibe blockiert es den optischen Fluss zwischen dem Empfänger und der LED. Der Sender erkennt Lichtunterbrechungen. Wenn die LED den Bereich mit abgenutzten Zähnen passiert, reagiert der Empfänger auf den Impuls und führt eine Synchronisation mit dem Steuergerät durch. |
Hallsensor | Das Sensordesign umfasst:
In einem Hall-Effekt-Kurbelwellensensor fließt Strom, wenn er sich einem sich ändernden Magnetfeld nähert. Beim Durchfahren von Bereichen mit verschlissenen Zähnen öffnet sich der Stromkreis des Kraftfeldes und das Signal wird an das elektronische Motorsteuergerät übermittelt. Arbeitet von einer unabhängigen Stromquelle. |
Wo sitzt der Sensor?
Lage des Positionssensors der Kurbelwelle: neben der Scheibe zwischen der Riemenscheibe der Lichtmaschine und dem Schwungrad. Für den freien Anschluss an das Bordnetz wird ein 50-70 cm langes Kabel mitgeliefert, an dem sich Anschlüsse für Schlüssel befinden. Am Sattel befinden sich Abstandshalter, um den Abstand auf 1-1,5 mm einzustellen.
Symptome und Ursachen von Störungen
Symptome eines defekten DPKV:
- der Motor springt nicht an oder bleibt nach einer Weile spontan stehen;
- keine Funken;
- Die ICE-Detonation tritt periodisch unter dynamischen Lasten auf;
- instabile Leerlaufdrehzahl;
- Motorleistung und Fahrdynamik werden reduziert;
- beim Wechseln des Modus tritt eine spontane Änderung der Drehzahl auf;
- Überprüfen Sie die Motorleuchte auf dem Armaturenbrett.
Die Symptome weisen auf die folgenden Gründe hin, warum der PCV-Sensor möglicherweise fehlerhaft ist:
- Kurzschluss zwischen Wicklungswindungen, mögliche Verzerrung des Signals über die Position des Kolbens bei UT und OT;
- das Kabel, das das DPKV mit dem Steuergerät verbindet, ist beschädigt - der Bordcomputer erhält keine ordnungsgemäße Benachrichtigung;
- Zahnfehler (Schrammen, Späne, Risse), der Motor springt möglicherweise nicht an;
- Das Eindringen von Fremdkörpern zwischen Zahnscheibe und Zähler oder Beschädigungen bei Arbeiten im Motorraum führen häufig zu einer Fehlfunktion des DPKV.
Probleme beim Starten des Motors
Varianten von Fehlfunktionen des Kurbelwellensensors, die den Betrieb des Verbrennungsmotors beeinträchtigen:
- Der Motor springt nicht an. Beim Drehen des Zündschlüssels dreht der Anlasser den Motor und die Kraftstoffpumpe brummt. Der Grund dafür ist, dass das Motorsteuergerät, ohne ein Signal vom Kurbelwellenpositionssensor zu erhalten, keinen korrekten Befehl ausgeben kann: an welchem Zylinder soll gestartet und an welchem die Düse geöffnet werden.
- Der Motor erwärmt sich auf eine bestimmte Temperatur und geht aus oder springt bei starkem Frost nicht an. Es gibt nur einen Grund - einen Mikroriss in der PKV-Sensorwicklung.
Instabiler Betrieb des Motors in verschiedenen Modi
Dies passiert, wenn das DPKV verschmutzt ist, insbesondere wenn Metallspäne oder Öl hineingelangen. Sogar ein leichter Stoß auf den magnetischen Mikrokreis des Zeitsensors ändert seinen Betrieb, da der Zähler sehr empfindlich ist.
Das Vorhandensein einer Detonation des Motors bei zunehmender Belastung
Der häufigste Grund ist der Ausfall des Messgeräts sowie ein Mikroriss in der Wicklung, der sich bei Vibration verbiegt, oder ein Riss im Gehäuse, in den Feuchtigkeit eindringt.
Anzeichen für Motorklopfen:
- Verletzung der Glätte des Verbrennungsprozesses des Kraftstoff-Luft-Gemisches in den Zylindern des Verbrennungsmotors;
- Springen auf den Empfänger oder die Auspuffanlage;
- Versagen;
- eine deutliche Reduzierung der Motorleistung.
Reduzierte Motorleistung
Die Motorleistung sinkt, wenn das Kraftstoff-Luft-Gemisch nicht rechtzeitig zugeführt wird. Ursache der Fehlfunktion ist die Delamination des Stoßdämpfers und die Verschiebung des Zahnsterns relativ zur Riemenscheibe. Die Motorleistung wird auch durch Schäden an der Wicklung oder am Gehäuse des Kurbelwellenpositionsmessers reduziert.
Wie kann man den Kurbelwellensensor selbst prüfen?
Sie können den Zustand des DPKV unabhängig untersuchen mit:
- Ohmmeter;
- Oszillograph;
- komplex, mit einem Multimeter, Megaohmmeter, Netzwerktransformator.
Wichtig zu wissen
Vor dem Austausch des Messgeräts wird außerdem empfohlen, eine vollständige Computerdiagnose des Verbrennungsmotors durchzuführen. Anschließend erfolgt eine äußere Inspektion, bei der Verschmutzungen oder mechanische Beschädigungen beseitigt werden. Und erst danach beginnen sie mit speziellen Geräten zu diagnostizieren.
Prüfung mit einem Ohmmeter
Bevor Sie mit der Diagnose fortfahren, schalten Sie den Motor aus und entfernen Sie den Steuerzeitensensor.
Schritt-für-Schritt-Anleitung zum Studium von DPKV mit einem Ohmmeter zu Hause:
- Installieren Sie ein Ohmmeter, um den Widerstand zu messen.
- Bestimmen Sie den Grad des Drosselwiderstands (berühren Sie die Testersonden an den Klemmen und klingeln Sie sie).
- Der zulässige Wert liegt zwischen 500 und 700 Ohm.
Verwendung eines Oszilloskops
Der Kurbelwellensensor wird bei laufendem Motor geprüft.
Aktionsalgorithmus mit einem Oszilloskop:
- Verbinden Sie den Tester mit dem Timer.
- Führen Sie ein Programm auf dem Bordcomputer aus, das die Messwerte eines elektronischen Geräts überwacht.
- Führen Sie mehrmals einen Metallgegenstand vor dem Kurbelwellensensor vorbei.
- Das Multimeter ist in Ordnung, wenn das Oszilloskop auf Bewegung reagiert. Wenn auf dem PC-Bildschirm keine Signale angezeigt werden, wird empfohlen, eine vollständige Diagnose durchzuführen.
Umfassender Check
Um es auszuführen, müssen Sie Folgendes haben:
- Megaohmmeter;
- Netztransformator;
- Induktivitätsmesser;
- Voltmeter (vorzugsweise digital).
Algorithmus der Aktionen:
- Vor Beginn eines vollständigen Scans muss der Sensor vom Motor entfernt, gründlich gewaschen, getrocknet und dann gemessen werden. Es wird nur bei Raumtemperatur durchgeführt, damit die Indikatoren genauer sind.
- Zunächst wird die Induktivität des Sensors (Induktionsspule) gemessen. Der Arbeitsbereich der numerischen Messungen sollte zwischen 200 und 400 MHz liegen.Wenn der Wert stark vom angegebenen Wert abweicht, ist wahrscheinlich der Sensor defekt.
- Als nächstes müssen Sie den Isolationswiderstand zwischen den Anschlüssen der Spule messen. Dazu wird ein Megaohmmeter verwendet, das die Ausgangsspannung auf 500 V einstellt. Es ist besser, den Messvorgang 2-3 Mal durchzuführen, um genauere Daten zu erhalten. Der gemessene Isolationswiderstandswert muss mindestens 0,5 MΩ betragen. Andernfalls kann ein Isolationsfehler in der Spule festgestellt werden (einschließlich der Möglichkeit eines Kurzschlusses zwischen Windungen). Dies weist auf einen Gerätefehler hin.
- Anschließend wird die Zeitscheibe mit einem Netztransformator entmagnetisiert.
Fehlerbehebung
Eine Reparatur des Sensors ist sinnvoll bei Störungen wie:
- Eindringen in den PKV-Kontaminationssensor;
- das Vorhandensein von Wasser im Sensoranschluss;
- Bruch der Schutzhülle von Kabeln oder Sensorkabelbäumen;
- Polaritätswechsel von Signalkabeln;
- keine Verbindung mit dem Kabelbaum;
- kurze Signalleitungen zur Sensormasse;
- verringertes oder vergrößertes Einbauspiel von Sensor und Synchronscheibe.
Tabelle: Arbeit mit kleineren Mängeln
Default | Mittel |
---|---|
Eindringen in den PKV-Sensor und Kontamination |
|
Vorhandensein von Wasser im Sensoranschluss |
|
Abschirmung oder Kabelbaum des Sensorkabels gebrochen |
|
Vertauschen Sie die Polarität der Signalkabel |
|
Der Sensor ist nicht mit dem Kabelbaum verbunden |
|
Sensorsignaldrähte mit Masse kurzgeschlossen |
|
Verringern oder Vergrößern des Einbauspiels des Sensors und der Synchronscheibe |
|
Wie wechselt man den Kurbelwellensensor?
Wichtige Nuancen, die beim Austausch des DPKV beachtet werden müssen:
- Vor der Demontage müssen Markierungen angebracht werden, die die Position des Bolzens relativ zum Sensor, dem DPKV selbst sowie die Markierung von Drähten und elektrischen Kontakten angeben.
- Beim Aus- und Einbau eines neuen PKV-Sensors ist auf einen guten Zustand der Taktscheibe zu achten.
- Ersetzen Sie das Messgerät mit Kabelbaum und Firmware.
Zum Austausch des PKV-Sensors benötigen Sie:
- neues Messgerät;
- automatischer Tester;
- Kavernometer;
- Schraubenschlüssel 10.
Algorithmus
Um den Kurbelwellenpositionssensor mit Ihren eigenen Händen zu wechseln, benötigen Sie:
- Schalten Sie die Zündung aus.
- Schalten Sie das elektronische Gerät stromlos, indem Sie die Klemmleiste von der Steuerung trennen.
- Lösen Sie mit einem Schraubenschlüssel die Schraube, mit der der Sensor befestigt ist, und entfernen Sie den fehlerhaften DPKV.
- Verwenden Sie einen Lappen, um die Landestelle von öligen Ablagerungen und Schmutz zu reinigen.
- Montieren Sie das neue Manometer mit den alten Befestigungselementen.
- Kontrollmessungen des Spalts zwischen den Zähnen der Antriebsriemenscheibe der Lichtmaschine und dem Sensorkern mit einem Messschieber durchführen. Der Abstand muss folgenden Werten entsprechen: 1,0 + 0,41 mm. Ist der Spalt bei der Kontrollmessung kleiner (größer) als der vorgegebene Wert, muss die Position des Sensors korrigiert werden.
- Prüfen Sie den Widerstand des Kurbelwellenpositionssensors durch einen Selbsttest. Für einen funktionierenden Sensor sollte er im Bereich von 550 bis 750 Ohm liegen.
- Setzen Sie den Bordcomputer zurück, um das Check-Engine-Signal auszuschalten.
- Schließen Sie den Kurbelwellenpositionssensor an das Stromnetz an (dafür ist ein Stecker eingebaut).
- Überprüfen Sie die Leistung des Elektrogeräts in verschiedenen Modi: im Ruhezustand und unter dynamischer Belastung.
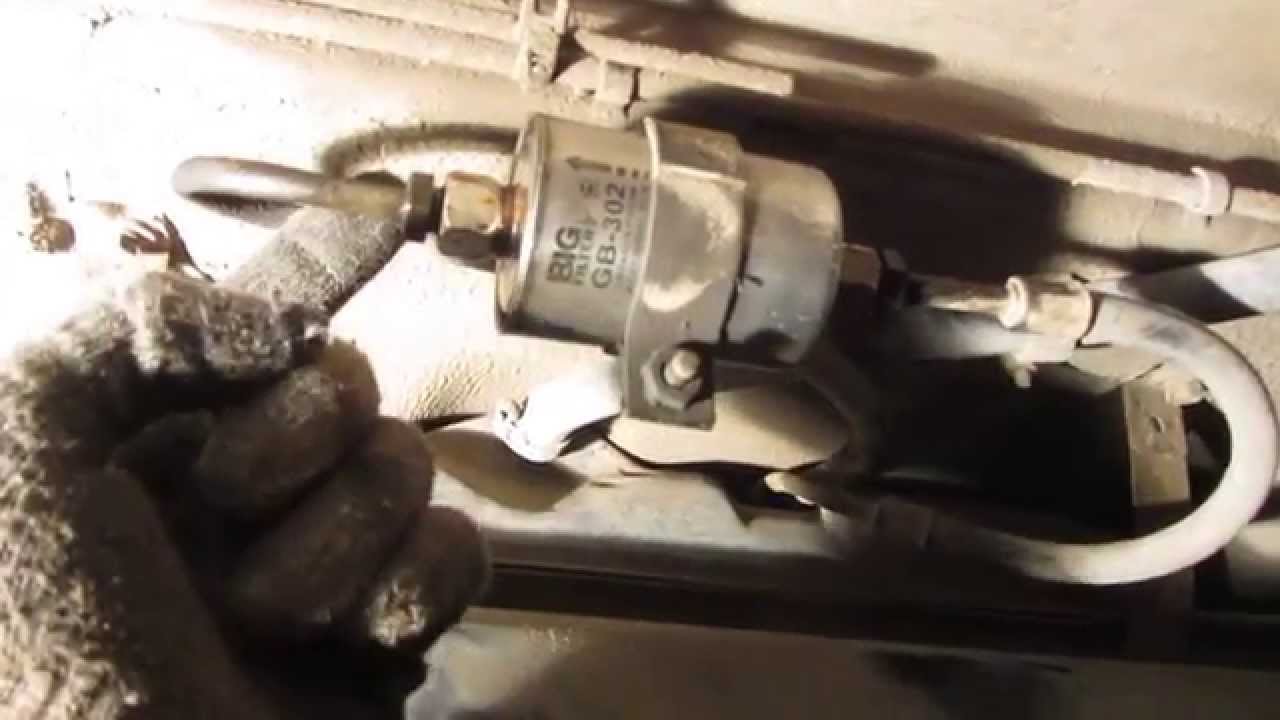
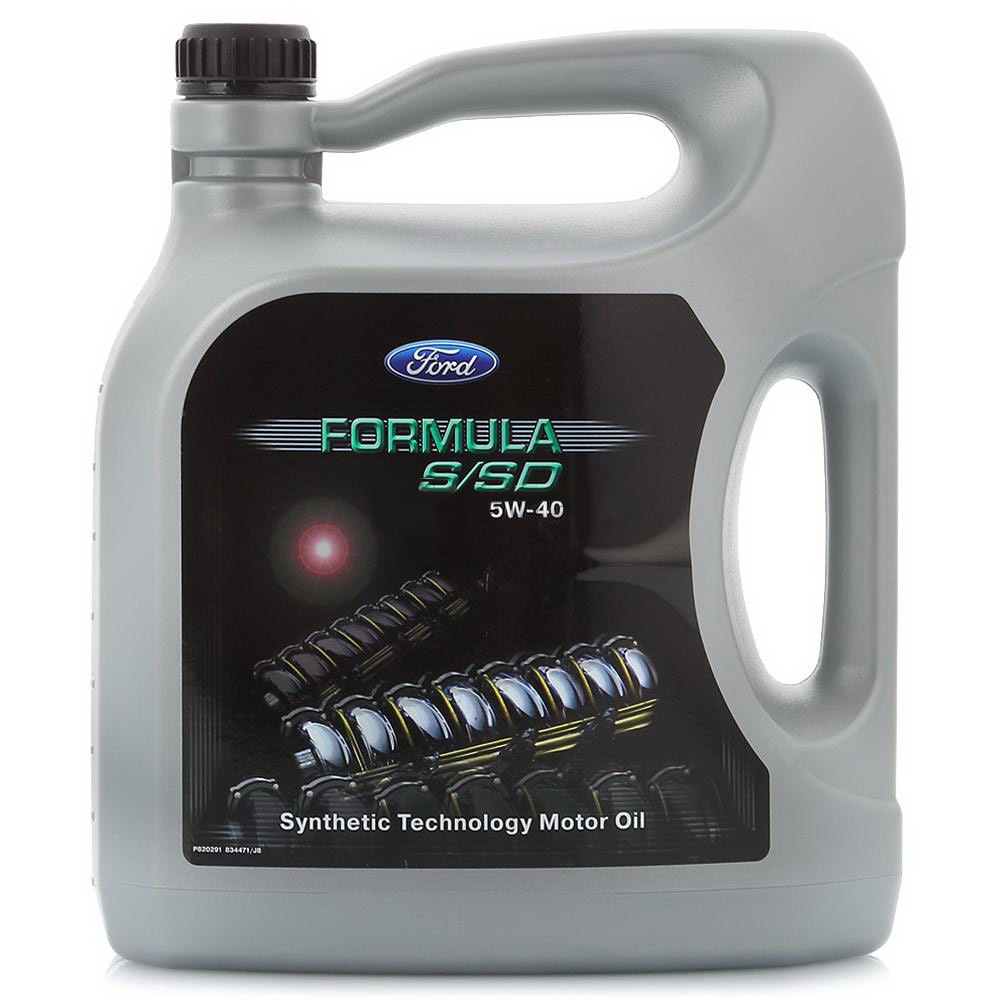