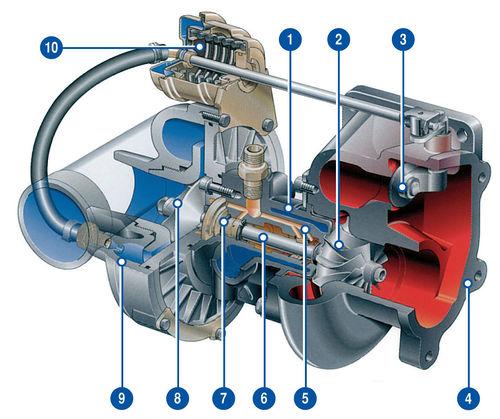
Betrieb von Turboladern
Turbolader werden üblicherweise zur Leistungssteigerung von Benzin- und Dieselmotoren eingesetzt. Ihre Haltbarkeit hängt von der richtigen Verwendung ab.
Turbolader werden üblicherweise zur Leistungssteigerung von Benzin- und Dieselmotoren eingesetzt. Ihr Funktionsprinzip besteht darin, die Abgasturbine mit einem Rotor zu verbinden, der die in die Zylinder eingespritzte Luft komprimiert.
Der Turbolader hat eine Reihe von Vorteilen, darunter einen einfachen Aufbau, den Verzicht auf einen zusätzlichen Antrieb und einen relativ geringen Herstellungsaufwand. Das Gerät hat auch Nachteile wie eine Verzögerung zwischen dem Gasgeben des Fahrers und dem Ansprechen der Turbine, die allgemein als „Turboverzögerung“ bezeichnet wird, und die Anfälligkeit für Fehlbedienungen. Turboloch verursacht die Unfähigkeit des Kompressors, sich unabhängig an Änderungen der Motordrehzahl und -last anzupassen. Es gibt bereits Lösungen, um die Anpassungsfähigkeit von Turboladern zu verbessern. Dabei handelt es sich um Bypassventile, die überschüssige Abgase zur Abgasseite leiten, und um technisch fortschrittlichere Turbolader mit variabler Turbinengeometrie.
In der Betriebspraxis kommt es für den Autonutzer vor allem auf die Kenntnis der Bedingungen an, die einen wesentlichen Einfluss auf die Dauer des störungsfreien Betriebs eines Turboladers haben. Erstens hat der Turboladerrotor eine bestimmte Masse und Abmessungen sowie ein damit verbundenes Massenträgheitsmoment. Während des Betriebs beschleunigt der Rotor auf eine Drehzahl von 100 - 120 U/min. Dies ist zehnmal schneller als ein Motor eines Formel-10-Autos. Daher ist der Turbinenrotor präzise ausgewuchtet und sein Lager schmiert das von der Förderpumpe des Motors gelieferte Öl. Beim Betrieb eines Turboladers ist neben der Wartung auch die Fahrtechnik von großer Bedeutung.
Um das Eindringen von Schmutz zu verhindern, muss die Ansaugluft durch regelmäßigen Filterwechsel sauber gehalten werden. Jede Ungleichgewichtsveränderung, wie etwa Schmutzablagerungen, bei diesen hohen Drehzahlen trägt zu vorzeitigem Lagerverschleiß bei. Besonderes Augenmerk sollte auf das Kühl- und Schmiermedium gelegt werden, wobei die Motorölwechselintervalle einzuhalten sind. Verwenden Sie außerdem kein Öl einer niedrigeren Qualitätsklasse als vom Autohersteller empfohlen. Versuche mit dem Wechsel der Ölsorte, Viskositätsklasse und Qualität wirken sich negativ auf den Motor und seine Aggregate aus. Eine Erhöhung des Ölverschmutzungsgrads sowie der Verlust seiner Schmier- und Schutzeigenschaften wirken sich negativ auf die Haltbarkeit der Lager und den Zustand des gesamten Motors aus. Bei Geräten mit hoher Laufleistung, die Öl „verbrauchen“, sollte der Stand regelmäßig überprüft und nachgefüllt werden.
Nach längerem Starten des Verbrennungsmotors (kürzer im Sommer, länger im Winter) fließt das Öl nicht zu verschiedenen Mechanismen, einschließlich der Kompressorlager. Während dieser Zeit werden sie aufgrund der Viskosität des Schmiermittels mit einer dünnen klebrigen Schicht geschmiert. Daher sollten nach dem Starten eines kalten Motors starke Gasbeschleunigungen und abrupte Starts vermieden werden. Diese Fahrweise führt dazu, dass die Lager für einige Zeit nicht ausreichend geschmiert werden, was ihre Lebensdauer verkürzt. Andererseits empfiehlt es sich, während der Fahrt nach dem Aufwärmen des Aggregats den Motor im mittleren und hohen Drehzahlbereich laufen zu lassen. Das ordnungsgemäße Abschalten des Motors ist für die Langlebigkeit des Kompressors sehr wichtig. Nach Beendigung der Fahrt hört die Ölpumpe auf zu arbeiten. Es versorgt die Lager der Turbine nicht mit einem Teil des Frischöls, deren beschleunigter Rotor mehrere Sekunden lang mit enormer Geschwindigkeit weiterdreht. Während dieser Zeit wird das Öl, das die Lager schmiert, sehr heiß, es kommt zu Verkohlungen, es bilden sich Partikel, die die präzise gefertigten Lagerlaufbahnen zerkratzen, was zu deren Zerstörung führt. Wenn Sie einen Turbomotor laufen lassen, warten Sie einige Sekunden, bevor Sie ihn abstellen. Zu diesem Zeitpunkt verlangsamt sich die Drehzahl der Turbine und das Risiko einer Beschädigung der Lager verringert sich.
Die Dauer des störungsfreien Betriebs eines Turboladers hängt maßgeblich von der Betriebsart ab. Allerdings ist zu betonen, dass es eine Reihe von Geräten gab, die von den Herstellern schlecht entwickelt wurden und nach relativ kurzer Laufzeit versagten. Ein typisches Anzeichen für einen Turboladerschaden sind deutlich spürbare Vibrationen am Einbauort. Bei schweren Schäden ist die Reibung von Metall auf Metall zu hören, eine große Menge weißer Rauch tritt aus dem Auspuffrohr aus, das Auto beschleunigt immer noch nicht.
Beschädigte Turbolader können regeneriert werden. Fachwerkstätten verfügen über entsprechende Kenntnisse, Erfahrungen und Reparatursätze. Die Kosten für eine typische Regeneration liegen je nach Größe der Turbine zwischen 800 und 2000 PLN und sind um ein Vielfaches niedriger als der Preis einer neuen Anlage.
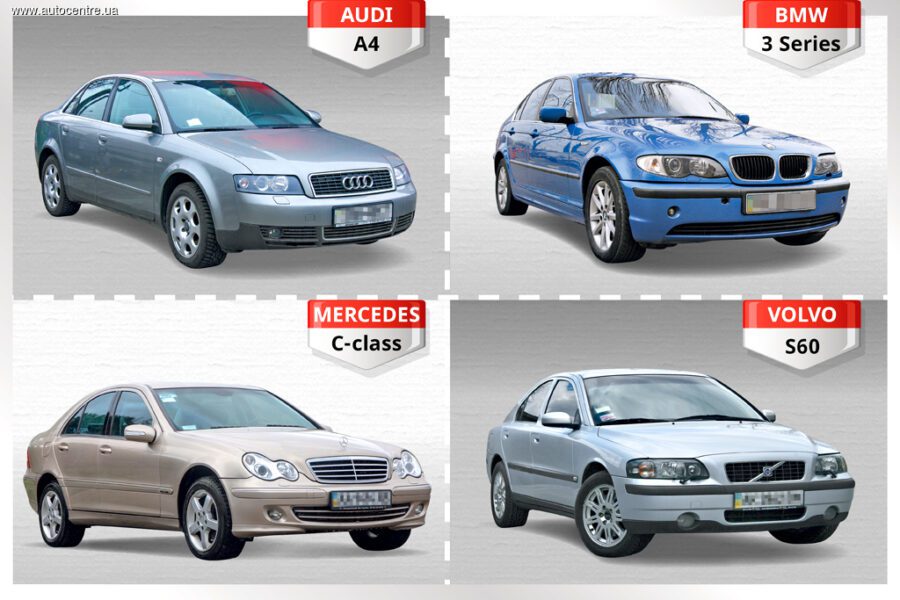
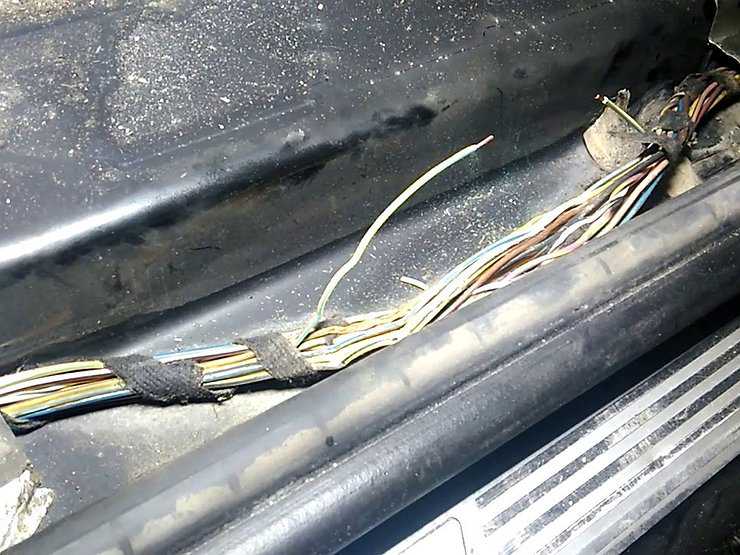