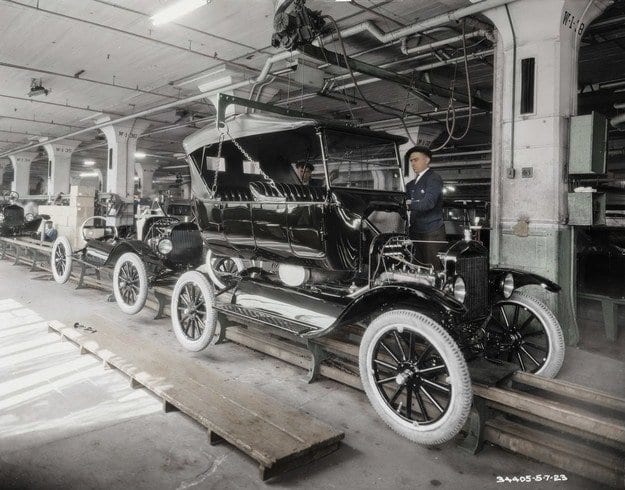
Wer hat den Förderer bewegt?
Die Produktionslinien funktionieren wieder, und dies ist ein Grund, sich an ihren Schöpfer zu erinnern
7. Oktober 1913 in einer der Hallen des Automobilwerks Highland Park. Ford startet die weltweit erste Autoproduktionslinie. Dieses Material ist Ausdruck des Respekts vor den innovativen Herstellungsverfahren von Henry Ford, der die Automobilindustrie revolutioniert hat.
Die Organisation der Autoproduktion ist heute ein sehr komplexer Prozess. Die Montage eines Autos im Werk macht 15 % des gesamten Produktionsprozesses aus. Die restlichen 85 Prozent betreffen die Produktion jedes einzelnen der mehr als zehntausend Teile und deren Vormontage in rund 100 der wichtigsten Produktionseinheiten, die dann ans Band gehen. Letzteres wird von einer großen Anzahl von Zulieferern (z. B. 40 bei VW) durchgeführt, die eine sehr komplexe und sehr effiziente aufeinander abgestimmte Kette von Produktionsprozessen durchführen, einschließlich genauer und rechtzeitiger Lieferungen (das sogenannte Just-in-Time-Verfahren). ) von Komponenten und Lieferanten. erste und zweite Ebene. Die Entwicklung jedes Modells ist nur ein Teil davon, wie es die Verbraucher erreicht. Eine große Anzahl von Ingenieuren ist an der Organisation des Produktionsprozesses beteiligt, der in einem Paralleluniversum stattfindet, einschließlich Aktionen von der Koordinierung der Lieferung von Komponenten bis zu ihrer physischen Montage in einer Fabrik mit Hilfe von Menschen und Robotern.
Die Entwicklung des Herstellungsverfahrens ist auf fast 110 Jahre Evolution zurückzuführen, aber Henry Ford hat den größten Beitrag zu seiner Entstehung geleistet. Es ist wahr, dass das Ford Model T, als er die aktuelle Organisation gründete, extrem einfach war und seine Komponenten fast vollständig von der Firma selbst hergestellt wurden, aber jeder Bereich der Wissenschaft hat seine Pioniere, die die Grundlagen fast blind legten . Henry Ford wird für immer als der Mann in die Geschichte eingehen, der Amerika motorisierte – lange bevor es in Europa geschah – indem er ein einfaches und zuverlässiges Auto mit einer effizienten Produktion kombinierte, die die Kosten senkte.
Пионер
Henry Ford glaubte immer, dass der menschliche Fortschritt von der natürlichen wirtschaftlichen Entwicklung auf der Grundlage der Produktion getrieben werden würde, und er hasste alle spekulativen Formen des Gewinns. Es überrascht nicht, dass der Gegner eines solchen wirtschaftlichen Verhaltens ein Maximalist sein wird, und das Streben nach Effizienz und die Schaffung einer Produktionslinie ist Teil seiner Erfolgsgeschichte.
In den Anfangsjahren der Automobilindustrie wurden Automobile von erfahrenen und normalerweise talentierten Ingenieuren in bescheidenen Handwerksbetrieben sorgfältig zusammengebaut. Zu diesem Zweck verwenden sie Maschinen, die bisher zur Montage von Wagen und Fahrrädern bekannt waren. Im Allgemeinen befindet sich die Maschine in einer statischen Position, und Arbeiter und Teile bewegen sich entlang der Maschine. Pressen, Bohrer und Schweißmaschinen werden an verschiedenen Orten gruppiert, und einzelne fertige Produkte und Komponenten werden auf Werkbänken montiert und müssen dann von einem Ort zum anderen und zum Auto selbst „fahren“.
Henry Fords Name kann nicht unter den Pionieren der Autoindustrie gefunden werden. Aber durch die kreative Kombination von Henry Fords einzigartigen Management-, Organisations- und Designfähigkeiten wurde das Automobil zu einem Massenphänomen und motorisierte die amerikanische Nation. Es verdankt ihm und Dutzenden anderer fortschrittlicher Amerikaner seinen privilegierten Status, und das Modell T des frühen XNUMX. Jahrhunderts verlieh dem heutigen Klischee, dass ein Auto eine Notwendigkeit sein kann, nicht unbedingt ein Luxus, einen greifbaren Charakter. Das Auto, das dabei die Hauptrolle spielt, das Modell T, glänzt nur mit unglaublicher Leichtigkeit und Stärke. Henry Fords Methoden zur Herstellung dieses Autos wurden jedoch zur Grundlage einer revolutionären neuen technischen Ideologie.
Bis 1900 gab es weltweit mehr als 300 Unternehmen, die Fahrzeuge mit Verbrennungsmotoren herstellten, und die führenden Länder in diesem Geschäft waren die USA, Frankreich, Deutschland, England, Italien, Belgien, Österreich und die Schweiz. Zu dieser Zeit entwickelte sich die Ölindustrie sehr schnell, und jetzt war Amerika nicht nur ein bedeutender Produzent von schwarzem Gold, sondern auch ein Technologieführer in diesem Bereich. Dies schafft eine ausreichend stabile Legierung, um die Entwicklung der amerikanischen Industrie zu verwerfen.
Amerikanisches Auto
Irgendwo in diesem Aufruhr erscheint der Name Henry Ford. 1903 gründete er seine eigene Firma, die er Ford Motor Company nannte, und wurde von den Partnern seines ersten Unternehmens wegen seines Wunsches, ein praktisches, zuverlässiges, billiges und serienmäßiges Auto herzustellen, abgelehnt. Ford baute ein Auto, um das Rennen zu gewinnen, setzte einen achttägigen Radfahrer hinter das Lenkrad und sammelte leicht 100 Dollar von wohlwollenden Investoren für sein Startup. Die Dodge-Brüder erklären sich bereit, ihn mit Motoren zu versorgen. 000 war er mit seinem ersten Serienauto fertig, das er Ford Model A nannte. Nachdem er mehrere teure Modelle auf den Markt gebracht hatte, beschloss er, zu seiner ursprünglichen Idee zurückzukehren, ein beliebtes Auto zu entwickeln. Durch den Kauf eines Teils der Aktien seiner Aktionäre erwirbt er genügend finanzielle Fähigkeiten und Positionen im Unternehmen, um seine eigene Produktion zu starten.
Ford ist selbst für das liberale Verständnis der Amerikaner ein seltener Vogel. Kitzlig, ehrgeizig, hatte er eigene Vorstellungen vom Automobilgeschäft, die sich damals deutlich von den Ansichten seiner Konkurrenten unterschieden. Im Winter 1906 mietete er ein Zimmer in seinem Werk in Detroit und verbrachte zwei Jahre damit, mit seinen Kollegen die Produktion des Modells T zu entwerfen und zu planen. Das Auto, das schließlich als Ergebnis der geheimen Arbeit des Ford-Teams entstand, veränderte sich . Bild von Amerika für immer. Für 825 US-Dollar kann ein Käufer des Model T ein Auto mit einem Gewicht von nur 550 kg und einem relativ leistungsstarken 20-PS-Vierzylindermotor erwerben, der dank eines pedalbetätigten Zweigang-Planetengetriebes leicht zu fahren ist. Einfach, zuverlässig und komfortabel, ein Kleinwagen begeistert die Menschen. Das Modell T war auch das erste amerikanische Auto, das aus leichterem Vanadiumstahl hergestellt wurde, was anderen Herstellern in Übersee zu dieser Zeit unbekannt war. Ford brachte dieses Verfahren aus Europa mit, wo es zur Herstellung von Luxuslimousinen verwendet wurde.
In den Anfangsjahren wurde das Model T wie alle anderen Autos produziert. Das wachsende Interesse daran und die wachsende Nachfrage veranlassten Ford jedoch, mit dem Bau eines neuen Werks zu beginnen und ein effizienteres Produktionssystem zu organisieren. Grundsätzlich sucht er keinen Kredit, sondern finanziert seine Unternehmungen aus eigenen Rücklagen. Der Erfolg des Autos ermöglichte es ihm, in die Schaffung eines einzigartigen Werks in Highland Park zu investieren, das von Rockefeller selbst benannt wurde und dessen Raffinerien das Kriterium für modernste Produktion "das industrielle Wunder seiner Zeit" sind. Fords Ziel ist es, das Auto so leicht und einfach wie möglich zu machen, und der Kauf neuer Teile ist rentabler als die Reparatur. Ein einfaches Modell T besteht aus einem Motor mit Getriebe, einem einfachen Rahmen und einer einfachen Karosserie sowie zwei Elementarachsen.
7 1913 Oktober,
In den Anfangsjahren wurde die Produktion in diesem vierstöckigen Werk von oben nach unten organisiert. Es "steigt" vom vierten Stock (wo der Rahmen zusammengebaut ist) in den dritten Stock, wo die Arbeiter Motoren und Brücken setzen. Nachdem der Zyklus im zweiten Stock endet, fahren neue Autos die letzte Rampe hinauf, vorbei an den Büros im ersten Stock. Die Produktion stieg in jedem der drei Jahre stark von 19 im Jahr 000 auf 1910 im Jahr 34 und erreichte 000 beeindruckende 1911 Einheiten. Und dies ist erst der Anfang, denn Ford droht bereits, "das Auto zu demokratisieren".
Er denkt darüber nach, wie er eine effizientere Produktion schaffen kann, und landet versehentlich in einem Schlachthaus, wo er eine mobile Linie zum Schneiden von Rindfleisch beobachtet. Das Schlachtfleisch wird an Haken aufgehängt, die sich entlang der Schienen bewegen, und an verschiedenen Stellen des Schlachthofs trennen Metzger es, bis nichts mehr übrig ist.
Dann kam ihm eine Idee, und Ford beschloss, den Prozess umzukehren. Mit anderen Worten bedeutet dies die Schaffung einer beweglichen Hauptproduktionslinie, die von zusätzlichen Linien angetrieben wird, die nach Vereinbarung angeschlossen werden. Zeit spielt eine Rolle - jede Verzögerung in einem der peripheren Elemente verlangsamt das Hauptelement.
Am 7. Oktober 1913 erstellte das Ford-Team in einer großen Fabrikhalle ein einfaches Montageband für die Endmontage, inklusive Winde und Kabel. An diesem Tag reihten sich 140 Arbeiter auf etwa 50 Metern der Produktionslinie aneinander, und die Maschine wurde mit einer Winde über den Boden gezogen. An jeder Arbeitsstation wird ein Teil der Struktur in einer fest definierten Reihenfolge hinzugefügt. Selbst mit dieser Innovation wird der Endmontageprozess von über 12 Stunden auf weniger als drei Stunden reduziert. Ingenieure übernehmen die Aufgabe, das Förderprinzip zu perfektionieren. Sie experimentieren mit allen möglichen Möglichkeiten – mit Schlitten, Trommelbahnen, Förderbändern, Schleppchassis an einem Seil und setzen Hunderte anderer Ideen um. Schließlich baute Ford Anfang Januar 1914 den sogenannten endlosen Kettenförderer, entlang dessen sich die Fahrgestelle zu den Arbeitern bewegten. Drei Monate später wurde das Man-High-System geschaffen, bei dem alle Teile und das Förderband auf Hüfthöhe angeordnet und so organisiert sind, dass die Arbeiter ihre Arbeit erledigen können, ohne ihre Beine zu bewegen.
Das Ergebnis einer brillanten Idee
Infolgedessen montierten bereits 1914 13 Arbeiter der Ford Motor Company 260 Autos in Zahlen und Worten. Zum Vergleich: In der übrigen Automobilindustrie produzieren 720 Arbeiter 66 Autos. 350 produzierte die Ford Motor Company 286 Model Ts, jeweils 770. Im Jahr 1912 stieg die Produktion des Model T auf 82 und der Preis fiel auf 388 $.
Viele werfen Ford vor, Menschen in Maschinen zu verwandeln, aber für Industrielle sieht das Bild ganz anders aus. Äußerst effektives Management und Entwicklung ermöglichen es denjenigen, die in der Lage sind, an der Organisation des Prozesses teilzunehmen, und weniger gebildeten und unterqualifizierten Arbeitnehmern - dem Prozess selbst. Um den Umsatz zu reduzieren, traf Ford eine mutige Entscheidung und erhöhte 1914 sein Gehalt von 2,38 USD pro Tag auf 1914 USD. Zwischen 1916 und 30, auf dem Höhepunkt des Ersten Weltkriegs, verdoppelte sich der Gewinn des Unternehmens von 60 Millionen auf XNUMX Millionen Dollar, die Gewerkschaften versuchten, sich in die Angelegenheiten von Ford einzumischen, und die Arbeiter wurden zu Käufern ihrer Produkte. Ihre Käufe bringen effektiv einen Teil der Löhne des Fonds zurück, und eine erhöhte Produktion hält den Wert des Fonds niedrig.
Schon 1921 hielt das Model T 60 % des Neuwagenmarktes. Zu dieser Zeit bestand Fords einziges Problem darin, mehr dieser Autos zu produzieren. Der Bau einer riesigen Hightech-Anlage beginnt, die eine noch effizientere Produktionsweise einführen wird – das Just-in-Time-Verfahren. Aber das ist eine andere Geschichte.
Text: Georgy Kolev
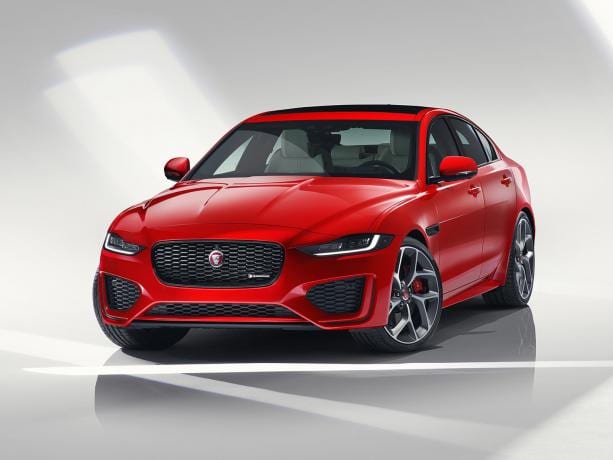
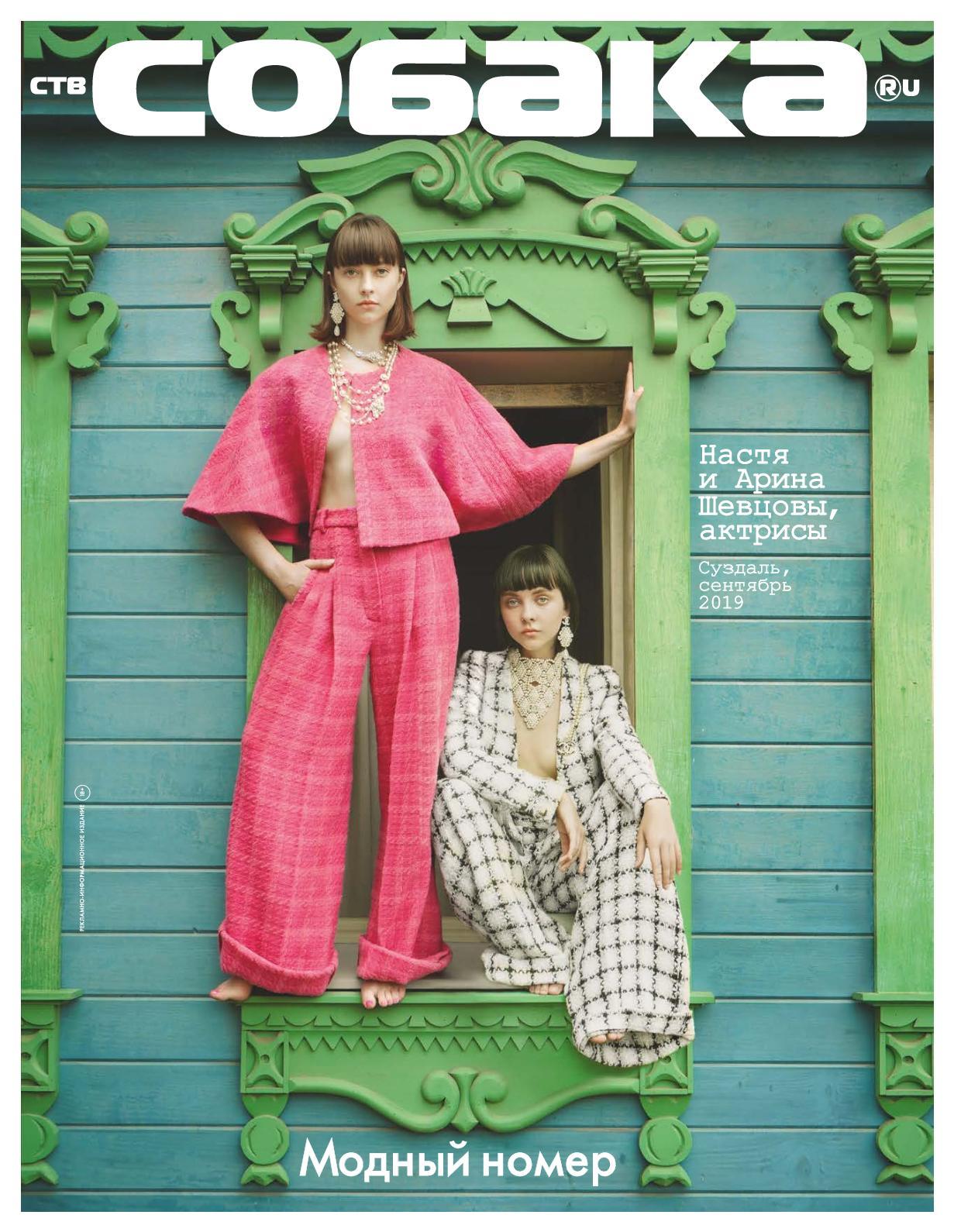