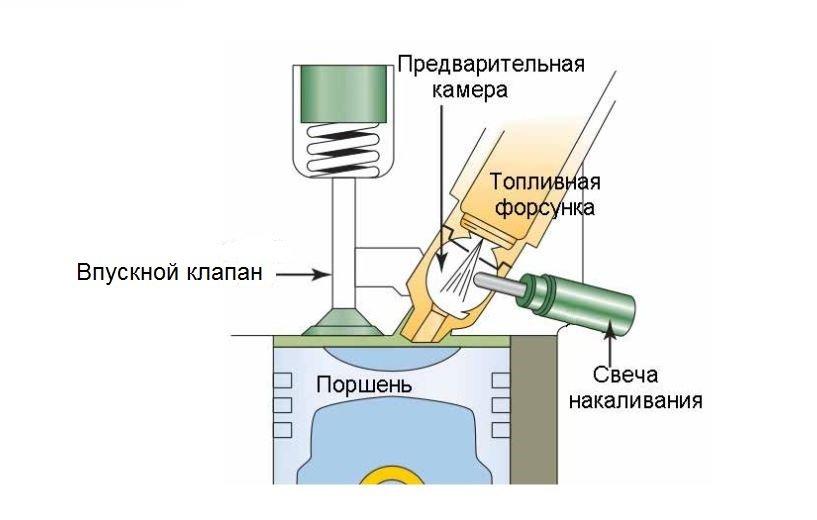
Diesel-Einspritzsysteme. Aufbau, Vor- und Nachteile
Im Gegensatz zu Benzinmotoren hatten Dieselmotoren von Anfang an eine Kraftstoffeinspritzung. Nur die Einspritzsysteme, Armaturen und der Druck des den Zylindern zugeführten Kraftstoffs änderten sich.
Das Arbeitsprinzip eines Dieselmotors, allgemein als Dieselmotor bekannt, unterscheidet sich grundlegend von dem eines Benzinmotors. Bei Tankwagen tritt das Kraftstoff-Luft-Gemisch oberhalb des Kolbens in den Brennraum ein. Nach der Kompression wird das Gemisch durch den Zusammenbruch eines elektrischen Funkens an den Elektroden der Zündkerze gezündet. Aus diesem Grund werden Ottomotoren auch Ottomotoren (SI-Motoren) genannt.
Bei Dieselmotoren komprimiert der Kolben in der Brennkammer nur Luft, die unter dem Einfluss eines enormen Drucks (mindestens 40 bar - daher der Name "Hochdruck") auf eine Temperatur von 600-800 ° C erhitzt wird. Das Einspritzen von Kraftstoff in diese heiße Luft führt zu einer sofortigen Selbstzündung des Kraftstoffs in der Verbrennungskammer. Aus diesem Grund werden Dieselantriebe auch als Kompressionszündungsmotoren (CI) bezeichnet. Sie wurden von Anfang an durch Einspritzen von Kraftstoff in den Brennraum und nicht in den Ansaugkrümmer versorgt, der den Motor nur mit Luft versorgt. Je nachdem, ob der Brennraum geteilt war oder nicht, wurden Dieselmotoren in Aggregate mit indirekter oder direkter Einspritzung unterteilt.
Indirekte Injektion
Diesel, obwohl er mit einem Direkteinspritzsystem debütierte, wurde nicht lange verwendet. Diese Lösung verursachte zu viele Probleme und wurde in der Automobilindustrie durch die 1909 patentierte indirekte Einspritzung ersetzt. Die Direkteinspritzung blieb in großen stationären und Schiffsmotoren sowie in einigen Lastwagen. Die Konstrukteure von Pkw bevorzugten Dieselmotoren mit indirekter Einspritzung, die einen ruhigeren Betrieb und weniger Geräusche aufweisen.
Der Begriff „indirekt“ bedeutet bei Dieselmotoren etwas ganz anderes als bei Ottomotoren, wo die indirekte Einspritzung das Einspritzen eines Luft-Kraftstoff-Gemisches in das Saugrohr ist. Bei Dieselmotoren mit indirekter Einspritzung gelangt wie bei Konstruktionen mit Direkteinspritzung auch der vom Injektor zerstäubte Kraftstoff in den Brennraum. Es ist nur in zwei Teile geteilt - einen Hilfsteil, in den Kraftstoff eingespritzt wird, und den Hauptteil, d. H. der Raum direkt über dem Kolben, in dem der Hauptprozess der Kraftstoffverbrennung stattfindet. Die Kammern sind durch einen Kanal oder Kanäle miteinander verbunden. Die Kammern sind in Form und Funktion in Vor-, Wirbel- und Luftreservoir unterteilt.
Letztere können nicht verwendet werden, da ihre Produktion praktisch eingestellt wurde. Bei Vorkammern und Drallkammern wird die Düse neben der Nebenkammer eingebaut und spritzt dort Kraftstoff ein. Dort erfolgt die Zündung, dann gelangt der teilweise verbrannte Kraftstoff in die Hauptkammer und brennt dort aus. Diesel mit Vorkammer oder Wirbelkammer laufen ruhig und können leichte Kurbelsysteme haben. Sie sind unempfindlich gegenüber der Kraftstoffqualität und können einfach gestaltete Düsen aufweisen. Sie sind jedoch weniger effizient als Diesel mit Direkteinspritzung, verbrauchen mehr Kraftstoff und haben Probleme beim Starten eines kalten Motors. Heute gehören Dieselmotoren mit indirekter Einspritzung in Pkw der Vergangenheit an und werden nicht mehr produziert. Sie sind heute selten in modernen Autos auf dem Markt zu finden. Sie sind nur in Designs wie dem indischen Hindustan und Tata, dem russischen UAZ, dem in Brasilien verkauften Mitsubishi Pajero der älteren Generation oder dem in Argentinien angebotenen Volkswagen Polo zu finden. Sie werden in viel größeren Mengen in Aftermarket-Fahrzeugen verwendet.
Direkte Injektion
Mit ihm fing alles an. Allerdings wurden die Vorteile der Direkteinspritzung zunächst nicht genutzt. Die Bedeutung der richtigen Verwirbelung des Kraftstoffs war nicht bekannt und seine Verbrennung war nicht optimal. Es bildeten sich Kraftstoffklumpen, die zur Rußbildung beitrugen. Die Prozesse am Kolben gingen zu schnell, die Motoren arbeiteten hart und zerstörten schnell das Kurbelwellenlager. Aus diesem Grund wurde die Direkteinspritzung aufgegeben und die indirekte Einspritzung bevorzugt.
Eine Rückkehr zu den Wurzeln, allerdings in einer modernen Version, erfolgte erst 1987, als der Fiat Croma 1.9 TD in die Serienproduktion ging. Die Direkteinspritzung erfordert eine effiziente Einspritzausrüstung, einen hohen Einspritzdruck, hochwertigen Kraftstoff und eine sehr starke (und daher schwere) Kurbelgarnitur. Es bietet jedoch einen hohen Wirkungsgrad und einen einfachen Start eines kalten Motors. Moderne Lösungen für Dieselmotoren mit Direkteinspritzung basieren hauptsächlich auf vollständig flachen Köpfen und Kolben mit entsprechend geformten Kammern (Hohlräumen). Die Kammern sind für die richtige Verwirbelung des Kraftstoffs verantwortlich. Die Direkteinspritzung ist heute in Pkw-Dieselmotoren weit verbreitet.
Direkteinspritzung - Pumpeninjektoren
Bei herkömmlichen Dieselmotoren sind verschiedene Arten von Pumpen für die Kraftstoffversorgung zuständig. In Pionierzeiten erfolgte die Kraftstoffeinspritzung mit Druckluft, in den 20er Jahren mit umgestalteten Ölpumpen. In den 300er Jahren waren bereits Spezialpumpen für Dieselmotoren weit verbreitet. Zunächst basierte es auf Serienpumpen, die Niederdruck (bis 60 bar) erzeugen. Erst in den 1000er Jahren kamen effizientere Axialverteilerpumpen (über 80 bar) auf. Mitte der siebziger Jahre erhielten sie eine mechanische Einspritzsteuerung, Mitte der achtziger Jahre eine elektronische Steuerung (BMW 524td, 1986).
Pump-Injektoren, die bereits in den 30er Jahren in Lastwagen eingesetzt wurden, waren eine etwas andere Art der Kraftstoffeinspritzung, sie wurden erstmals 1998 vom Volkswagen-Konzern in Pkw eingesetzt (Passat B5 1.9 TDI). Kurz gesagt ist ein Pumpinjektor ein Injektor mit eigener Pumpe, die von einer Nockenwelle angetrieben wird. Somit ist der gesamte Vorgang des Bedruckens und Einspritzens in den Zylinder auf den Zylinderkopf beschränkt. Das System ist sehr kompakt, es gibt keine Kraftstoffleitungen, die die Pumpe mit den Einspritzdüsen verbinden. Daher gibt es keine Düsenpulsation, was es schwierig macht, die Kraftstoffdosis zu regulieren und undicht zu werden. Da der Kraftstoff in der Einspritzdüsenkammer teilweise verdampft, kann der Einspritzzeitpunkt klein sein (einfacher Start). Am wichtigsten ist jedoch der sehr hohe Einspritzdruck von 2000-2200 bar. Die Kraftstoffdosis im Zylinder vermischt sich schnell mit Luft und verbrennt sehr effizient.
Im Allgemeinen zeichnet sich ein Pumpe-Düse-Dieselmotor durch einen hohen Wirkungsgrad, einen geringen Kraftstoffverbrauch, eine hohe Drehzahl und die Möglichkeit aus, eine hohe Leistungsdichte zu erzielen. Aber ein Einheitseinspritzmotor ist teuer in der Herstellung, hauptsächlich aufgrund der Komplexität des Zylinderkopfs. Seine Arbeit ist hart und laut. Beim Antrieb mit Pumpe-Düse-Einheiten treten auch Emissionsprobleme auf, was wesentlich dazu beigetragen hat, dass VW diese Lösung aufgegeben hat.
Direkteinspritzung - Common Rail
Das wichtigste Element des Common-Rail-Einspritzsystems ist das „Common Rail“, eine Art Tank, auch „Druckspeicher“ genannt, in den eine Pumpe Dieselkraftstoff pumpt. Es tritt nicht direkt von der Pumpe, sondern vom Tank in die Düsen ein, während für jeden Zylinder der gleiche Druck aufrechterhalten wird.
Bildlich können wir sagen, dass jeder der Injektoren nicht auf eine Portion Kraftstoff von der Pumpe wartet, sondern immer noch Kraftstoff mit einem sehr hohen Druck hat. Die elektrischen Impulse, die die Injektoren ansteuern, reichen aus, um den Brennräumen Kraftstoff zuzuführen. Mit einem solchen System können Sie mehrphasige Einspritzungen (sogar 8 Phasen pro Einspritzung) erstellen, was zu einer sehr präzisen Kraftstoffverbrennung mit allmählichem Druckanstieg führt. Der sehr hohe Einspritzdruck (1800 bar) ermöglicht die Verwendung von Injektoren mit sehr kleinen Öffnungen, die den Kraftstoff fast in Form eines Nebels abgeben.
All dies wird ergänzt durch hohe Motoreffizienz, Laufruhe und Geräuscharmut (trotz Direkteinspritzung), gute Manövrierbarkeit und geringe Abgasemissionen. Common-Rail-Motoren erfordern jedoch den hochwertigsten Kraftstoff und die besten Filter. Verunreinigungen im Kraftstoff können Einspritzdüsen zerstören und Schäden verursachen, deren Reparatur äußerst kostspielig ist.
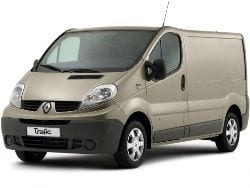
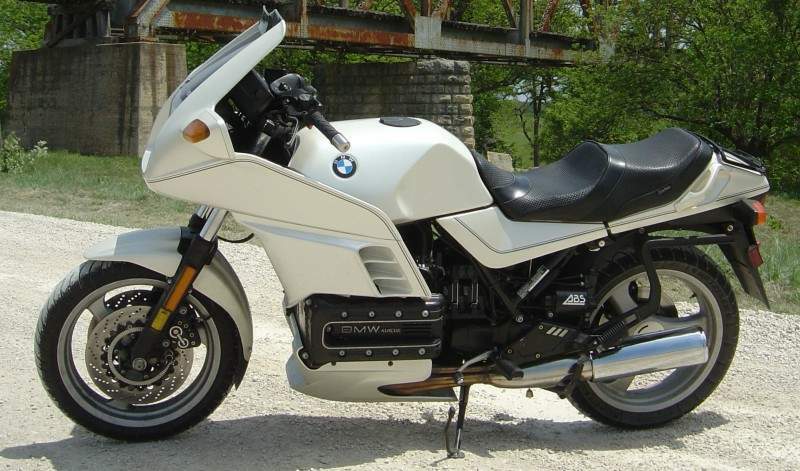