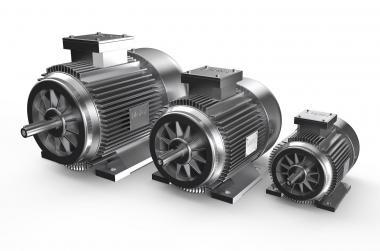
Stationärer Motor
Obwohl die romantische Ära der Dampflokomotive längst vorbei ist, sehnen wir uns nach den alten Zeiten, in denen wir Kutschen sehen konnten, die von riesigen, prächtigen Lokomotiven gezogen wurden, heiße Dampfwalzen, die den Straßenkies aufwühlten, oder rauchende Lokomotiven, die auf den Feldern arbeiteten.
Eine einzelne stationäre Dampfmaschine trieb über ein Riemenantriebssystem alle Fabrikmaschinen oder Webstühle zentral an. Ihr Kessel verbrannte gewöhnliche Kohle.Es mag schade sein, dass wir solche Maschinen außerhalb des Museums nicht sehen, aber es ist möglich, ein Holzmodell einer stationären Maschine zu bauen. к Es ist eine große Freude, so ein Holzmobile, ein mobiles Arbeitsgerät, zu Hause zu haben. Dieses Mal werden wir ein Modell einer komplexeren Dampfmaschine mit einer Schiebesynchronisierung als zuvor bauen. Für den Antrieb des Holzmodells nutzen wir selbstverständlich statt Dampf Druckluft aus einem Haushaltskompressor.
Betrieb der Dampfmaschine Dabei wird komprimierter Wasserdampf, in unserem Fall komprimierte Luft, entweder auf der einen oder anderen Seite des Kolbens in den Zylinder abgegeben. Dadurch entsteht eine variable Gleitbewegung des Kolbens, die über die Pleuelstange und die Antriebswelle auf das Schwungrad übertragen wird. Die Pleuelstange wandelt die Hin- und Herbewegung des Kolbens in die Drehbewegung des Schwungrads um. Eine Schwungradumdrehung wird in zwei Kolbenhüben erreicht. Die Dampfverteilung erfolgt über einen Schiebemechanismus. Das Timing wird durch einen Exzenter eingestellt, der auf derselben Achse wie das Schwungrad und die Kurbel montiert ist. Der Flachschieber verschließt und öffnet die Durchlässe zum Einleiten von Dampf in den Zylinder und ermöglicht gleichzeitig das Ausstoßen von verbrauchtem expandiertem Dampf.
Werkzeuge: Trichinensäge, Metallsägeblatt, elektrische Bohrmaschine auf Ständer, Bohrmaschine auf Werkbank montiert, Bandschleifer, Exzenterschleifer, Dremel mit Holzaufsätzen, Stichsäge, Klebepistole mit Heißkleber, Tischlerbohrer 8, 11 und 14 mm. Auch Holzschaber oder Feilen können nützlich sein. Um das Modell anzutreiben, verwenden wir einen Heimkompressor oder einen sehr leistungsstarken Staubsauger, dessen Düse Luft bläst.
Material: Kiefernbrett 100 mm breit und 20 mm dick, Rollen mit einem Durchmesser von 14 und 8 mm, Brett 20 x 20 mm, Brett 30 x 30 mm, Brett 60 x 8 mm, Sperrholz 4 und 10 mm dick. Holzschrauben, Nägel 20 und 40 mm. Klarlack im Spray. Silikonfett oder Maschinenöl.
Maschinenbasis. Es hat Abmessungen von 450 x 200 x 20 mm. Machen wir es aus zwei Stücken Kiefernbrettern und kleben sie mit ihren längeren Seiten zusammen, oder aus einem Stück Sperrholz. Eventuelle Unebenheiten auf dem Brett und nach dem Schneiden verbleibende Stellen sollten mit Schleifpapier geglättet werden.
Schwungradachshalterung. Es besteht aus einem vertikalen Brett und einer darüber liegenden Planke. Das Loch für die Holzachse wird an der Stelle gebohrt, an der sich ihre Flächen nach dem Zusammenschrauben berühren. Wir benötigen zwei Sätze identischer Elemente. Wir schneiden Stützen aus Kiefernbrettern mit den Maßen 150 x 100 x 20 mm und Latten mit einem Querschnitt von 20 x 20 und einer Länge von 150 mm. Bohren Sie in die Lamellen im Abstand von 20 mm von den Kanten Löcher mit einem Durchmesser von 3 mm und bohren Sie diese mit einem 8 mm Bohrer auf, damit die Schraubenköpfe gut verdeckt werden können. Außerdem bohren wir Löcher mit einem Durchmesser von 3 mm in die Vorderseite der Dielen, damit die Dielen verschraubt werden können. Bohren Sie an der Kontaktstelle mit einem 14-mm-Bohrer Löcher für die Schwungradachse. Beide Elemente werden sorgfältig mit Schleifpapier, vorzugsweise einem Exzenterschleifer, bearbeitet. Vergessen Sie auch nicht, die Löcher für die Holzachse der Walze mit gerolltem Schleifpapier zu reinigen. Die Achse sollte sich mit minimalem Widerstand drehen. Die so entstandenen Träger werden zerlegt und mit farblosem Lack überzogen.
Schwungrad. Wir beginnen damit, die Struktur eines Kreises auf Normalpapier zu zeichnen.Unser Schwungrad hat einen Gesamtdurchmesser von 200 mm und sechs Speichen. Sie werden so erstellt, dass wir sechs Rechtecke auf dem Kreis zeichnen, die um 60 Grad relativ zur Kreisachse gedreht sind. Zeichnen wir zunächst einen Kreis mit einem Durchmesser von 130 mm und markieren dann die Speichen mit einer Dicke von 15 mm.. In die Ecken der resultierenden Dreiecke zeichnen wir Kreise mit einem Durchmesser von 11 mm. Legen Sie das Papier mit der gezeichneten Kreisstruktur auf das Sperrholz und markieren Sie zunächst mit einem Locher die Mittelpunkte aller kleinen Kreise sowie den Mittelpunkt des Kreises. Diese Dellen gewährleisten die Bohrgenauigkeit. Zeichnen Sie den Kreis, die Nabe und das Rad dort, wo die Speichen an einem Paar Bremssätteln enden, direkt auf das Sperrholz. Wir bohren alle Ecken der Dreiecke mit einem Bohrer mit einem Durchmesser von 11 mm. Markieren Sie mit einem Bleistift die Bereiche auf dem Sperrholz, die leer sein sollen. Das erspart uns Fehler. Mit einer Stichsäge oder einer Trichomsäge können wir das vormarkierte, überschüssige Material vom Schwungrad abschneiden, was zu effektiven Stricknadeln führt. Mit einer Feile oder einem zylindrischen Fräser, einem Abstreifer und anschließend einem Dremel glätten wir mögliche Ungenauigkeiten und schrägen die Kanten der Speichen ab.
Schwungradfelge. Wir benötigen zwei identische Felgen, die wir auf beide Seiten des Schwungrads kleben. Wir werden sie auch aus 10 mm dickem Sperrholz schneiden. Die Räder haben einen Außendurchmesser von 200 mm. Wir zeichnen sie mit einem Zirkel auf Sperrholz und schneiden sie mit einer Stichsäge aus. Dann zeichnen wir koaxial einen Kreis mit einem Durchmesser von 130 mm und schneiden dessen Mittelpunkt aus. Dies wird der Rand des Schwungrads sein, also sein Rand. Der Kranz soll mit seinem Gewicht die Trägheit des rotierenden Rades erhöhen. Mit Wikol-Kleber bedecken wir das Schwungrad, d.h. das mit Stricknadeln, mit Kränzen auf beiden Seiten. Bohren Sie ein 6-mm-Loch in die Mitte des Schwungrads, um eine M6-Schraube in die Mitte einzuführen. So erhalten wir eine improvisierte Drehachse des Rades. Nachdem wir diese Schraube als Radachse in die Bohrmaschine eingebaut haben, bearbeiten wir das Spinnrad schnell, zuerst mit grobem und dann mit feinem Schleifpapier. Ich rate Ihnen, die Drehrichtung der Bohrmaschine zu ändern, damit sich die Radschraube nicht löst. Das Rad sollte glatte Kanten haben und sich nach der Bearbeitung auf unserer Pseudodrehmaschine reibungslos drehen lassen, ohne seitlich anzustoßen. Dies ist ein sehr wichtiges Kriterium für die Qualität des Schwungrades. Sobald dieses Ziel erreicht ist, entfernen Sie die provisorische Schraube und bohren Sie ein 14-mm-Achsenloch.
Maschinenzylinder. Hergestellt aus 10 mm Sperrholz. Wir beginnen mit einem 140 x 60 mm großen Unter- und Oberteil sowie einem 60 x 60 mm großen Rück- und Vorderteil. Bohren Sie 14-mm-Löcher in die Mitte dieser Quadrate. Diese Elemente kleben wir mit Heißkleber aus einer Klebepistole zusammen und schaffen so eine Art Zylinderrahmen. Die entsprechenden Teile müssen senkrecht und parallel zueinander befestigt werden. Verwenden Sie daher beim Kleben einen Winkel und halten Sie diese in Position, bis der Kleber aushärtet. Beim Kleben empfiehlt es sich, die Rolle, die als Kolbenstange dient, in die Löcher des Hinter- und Vorderteils einzuführen. Von der Genauigkeit dieser Verklebung hängt die künftige einwandfreie Funktion des Modells ab.
Der Kolben. Hergestellt aus 10 mm dickem Sperrholz, Abmessungen 60 x 60 mm. Schleifen Sie die Kanten des Quadrats mit feinem Schleifpapier ab und fasen Sie die Seiten ab. Bohren Sie ein 14-mm-Loch in den Kolben für die Kolbenstange. In die Oberseite des Kolbens wird senkrecht ein Loch mit einem Durchmesser von 3 mm für eine Schraube gebohrt, mit der der Kolben an der Kolbenstange befestigt wird. Bohren Sie mit einem 8-mm-Bohrer ein Loch, um den Schraubenkopf zu verbergen. Die Schraube geht durch die Kolbenstange und hält den Kolben an Ort und Stelle.
Kolbenstange. Schneiden wir einen Zylinder mit einem Durchmesser von 14 mm aus. Seine Länge beträgt 280 mm. Wir setzen den Kolben auf die Kolbenstange und bauen ihn in den Kolbenrahmen ein. Zunächst ermitteln wir jedoch die Position des Kolbens relativ zur Kolbenstange. Der Kolben bewegt sich um 80 mm. Beim Gleiten sollte es nicht bis zu den Kanten der Kolbeneinlass- und -auslassöffnungen reichen, aber in der neutralen Position sollte es sich in der Mitte des Zylinders befinden und die Kolbenstange sollte nicht aus der Vorderseite des Zylinders herausfallen. Wenn wir diese Stelle gefunden haben, markieren wir mit einem Bleistift die Position des Kolbens im Verhältnis zur Kolbenstange und bohren schließlich ein Loch mit einem Durchmesser von 3 mm hinein.
Verteilung. Dies ist der komplexeste Teil unserer Maschine. Wir müssen die Luftkanäle vom Kompressor zum Zylinder, von einer Seite zur anderen Seite des Kolbens und dann von der Abluft aus dem Zylinder nachbilden. Wir werden diese Kanäle aus mehreren Schichten 4 mm dickem Sperrholz herstellen. Der Zahnriemen besteht aus fünf Platten mit den Maßen 140 x 80 mm. In jeder Platte werden Löcher gemäß den auf dem Foto gezeigten Formen ausgeschnitten. Beginnen wir damit, die benötigten Details auf Papier zu zeichnen und alle Details auszuschneiden. Wir zeichnen die Muster der Fliesen mit einem Filzstift auf das Sperrholz und ordnen sie so an, dass kein Material verschwendet wird und gleichzeitig möglichst wenig Arbeitsaufwand beim Sägen entsteht. Markieren Sie sorgfältig die markierten Stellen für die Hilfslöcher und schneiden Sie die entsprechenden Formen mit einer Stichsäge oder einem Dreifuß aus. Zum Schluss nivellieren wir alles und reinigen es mit Schleifpapier.
Reißverschluss. Dies ist eine Sperrholzplatte mit der gleichen Form wie auf dem Foto. Bohren Sie zunächst die Löcher und schneiden Sie diese mit einer Stichsäge aus. Das verbleibende Material kann mit einer Trichomsäge geschnitten oder mit einem konischen zylindrischen Cutter oder Dremel entsorgt werden. Auf der rechten Seite des Schlittens befindet sich ein Loch mit einem Durchmesser von 3 mm, in dem sich die Achse des Exzenterhebelgriffs befindet.
Gleitführungen. Der Schieber arbeitet zwischen zwei Läufern, der unteren und der oberen Führung. Wir fertigen sie aus Sperrholz oder Latten mit einer Dicke von 4 mm und einer Länge von 140 mm. Kleben Sie die Führungen mit Vicol-Kleber auf die entsprechende nächste Zeitscheibe.
Pleuelstange. Wir schneiden es in die traditionelle Form, wie auf dem Foto gezeigt. Wichtig ist der Achsabstand der Löcher mit einem Durchmesser von 14 mm. Es sollte 40 mm betragen.
Kurbelarm. Es besteht aus einem Streifen von 30 x 30 mm und hat eine Länge von 50 mm. Wir bohren ein 14-mm-Loch in den Block und ein Sackloch senkrecht zur Vorderseite. Schleifen Sie das andere Ende des Blocks mit einer Holzfeile sowie einem Schleifgerät und Schleifpapier ab.
Kolbenstangengriff. Es ist U-förmig, besteht aus 30 x 30 mm Holz und hat eine Länge von 40 mm. Seine Form können Sie auf dem Foto erkennen. Wir bohren ein 14-mm-Loch in die Vorderseite des Blocks. Machen Sie mit einer Säge mit Sägeblatt zwei Schnitte und bohren Sie mit einer Bohrmaschine und einer Trichinensäge einen Schlitz für die Kolbenstange hinein. Wir bohren ein Loch für die Achse, die die Kurbel mit der Kolbenstange verbindet.
Zylinderunterstützung. Wir benötigen zwei identische Elemente. Schneiden Sie die Stützen aus Kiefernbrettern mit den Maßen 90 x 100 x 20 mm.
Exzentrizität. Schneiden Sie aus 4 mm dickem Sperrholz vier Rechtecke mit den Maßen jeweils 40 x 25 mm aus. Wir bohren mit einem 14-mm-Bohrer Löcher in die Rechtecke. Das exzentrische Design ist auf dem Foto zu sehen. Diese Löcher befinden sich entlang der Längsachse, sind jedoch entlang der Querachse um 8 mm gegeneinander versetzt. Wir verbinden die Rechtecke zu zwei Paaren und kleben sie mit ihren Flächen zusammen. Kleben Sie einen 28 mm langen Zylinder in die Innenlöcher. Stellen wir sicher, dass die Flächen der Rechtecke parallel zueinander sind. Ein Türdrücker kann uns dabei helfen.
HebelVerbindung des Schiebers mit dem Exzenter. Es besteht aus drei Teilen. Der erste ist ein U-förmiger Griff mit Schieber. In der Ebene wird ein Loch für die Achse gebohrt, entlang derer es eine Schaukelbewegung ausführt. Am anderen Ende ist eine Exzenterklemme aufgeklebt. Diese Klemme ist zerlegbar und besteht aus zwei Blöcken mit den Maßen jeweils 20x20x50 mm. Verbinden Sie die Blöcke mit Holzschrauben und bohren Sie dann am Rand der Rippe ein 14-mm-Loch für die Exzenterwelle. Wir bohren in einen der Blöcke senkrecht zur Achse ein Sackloch mit einem Durchmesser von 8 mm. Jetzt können wir beide Teile mit einer Welle mit einem Durchmesser von 8 mm und einer Länge von etwa 160 mm verbinden, wichtig ist jedoch der Abstand zwischen den Achsen dieser Teile, der 190 mm betragen sollte.
Maschinenmontage. Montieren Sie den Kolben mit einer Schraube an der in den Zylinderrahmen eingesetzten Kolbenstange und bohren Sie am Ende ein Loch für die Achse der Handkurbel. Denken Sie daran, dass das Loch parallel zur Basis sein muss. Kleben Sie die folgenden Steuertriebselemente auf den Zylinderrahmen (Foto a). Die nächste erste Platte mit vier Löchern (Foto b), die zweite mit zwei großen Löchern (Foto c) verbindet die Löcher zu zwei Paaren. Als nächstes ist die dritte Platte (Foto d) mit vier Löchern und legen Sie den Schieber darauf. Die Aufnahmen (Foto e und f) zeigen, dass der im Betrieb durch den Exzenter verschobene Schieber nacheinander das eine oder andere Lochpaar freigibt. Kleben Sie die beiden Führungen, die den Schieber führen, von oben und unten auf die dritte Platte. Wir befestigen die letzte Platte mit zwei Löchern daran und bedecken den Schieber von oben (Foto d). Kleben Sie den Block mit dem Durchgangsloch auf das obere Loch mit einem solchen Durchmesser, dass Sie den Druckluftversorgungsschlauch daran befestigen können. Auf der anderen Seite wird der Zylinder mit einem mit mehreren Schrauben aufgeschraubten Deckel verschlossen. Kleben Sie die Schwungradachsenträger auf die Basis und achten Sie darauf, dass sie in einer Linie und parallel zur Ebene der Basis liegen. Vor der vollständigen Montage lackieren wir die Elemente und Komponenten der Maschine mit einem farblosen Lack. Wir setzen das Pleuel auf die Schwungradachse und kleben es genau senkrecht dazu. Setzen Sie die Pleuelachse in das zweite Loch ein. Beide Achsen müssen parallel zueinander sein. Kleben Sie auf der anderen Seite der Basis zwei Bretter, um eine Stütze für den Zylinder zu bilden. Wir kleben einen kompletten Zylinder mit einem Steuermechanismus darauf. Nachdem der Zylinder geklebt ist, installieren Sie den Hebel, der den Schieber mit dem Exzenter verbindet. Erst jetzt können wir die Länge des Hebels bestimmen, der die Pleuelkurbel mit der Kolbenstange verbindet. Schneiden Sie den Schaft richtig aus und kleben Sie die U-förmigen Griffe fest.Wir verbinden diese Elemente mit Äxten aus Nägeln. Der erste Versuch besteht darin, die Schwungradachse von Hand zu drehen. Alle beweglichen Teile müssen sich ohne übermäßigen Widerstand bewegen. Die Kurbel macht eine Umdrehung und die Spule sollte mit einer exzentrischen Verschiebung reagieren.
Spiel. Schmieren Sie die Maschine dort mit Öl, wo Reibung auftreten soll. Abschließend verbinden wir das Modell mit einem Kabel mit dem Kompressor. Nach dem Starten des Geräts und dem Zuführen von Druckluft in den Zylinder sollte unser Modell problemlos starten und dem Konstrukteur viel Freude bereiten. Eventuelle Lecks können mit Kleber aus einer Klebepistole oder klarem Silikon abgedichtet werden, aber dadurch wird unser Modell unauslöschlich. Ein wertvoller Vorteil ist die Tatsache, dass das Modell zerlegt werden kann, um beispielsweise die Bewegung eines Kolbens in einem Zylinder zu demonstrieren.
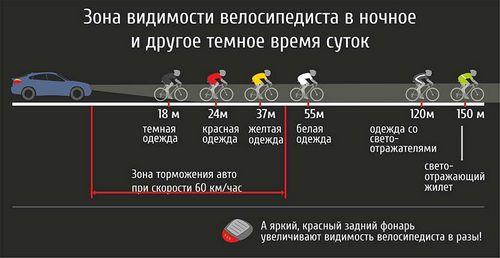
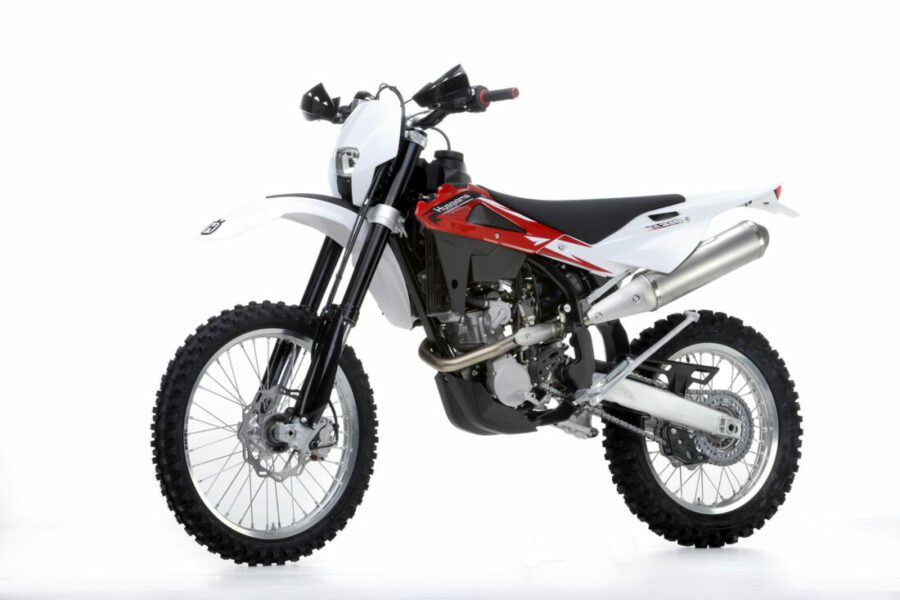